Stainless steel or steel with anti-corrosion coating
At Beritch, we specialize in the manufacture of stainless steel and anti-corrosion coated steel, two essential materials for ensuring the protection of steel against corrosion in industrial sectors such as automotive, naval, petrochemical, and food. Our experience in steel treatment allows us to offer advanced solutions tailored to each environment.
In addition to stainless steel, we develop steel with anti-corrosion coatings, designed to maximize its resistance under extreme conditions. To achieve this, we apply anti-corrosion coatings based on protective paints, polymers, and metallic coatings such as galvanizing and anodizing.
Both options offer key advantages in preventing rust and deterioration of the metal. At Beritch, we not only manufacture high-quality steel, but also advise our clients on the selection of the most appropriate anti-corrosion treatment based on the conditions of use, ensuring greater durability and performance in their projects.
Protective anti-corrosion coating for steel
Why is corrosion protection of steel important?
Steel is a fundamental material in various industries, but its exposure to moisture, chemicals, and extreme environmental conditions can cause its progressive deterioration. At Beritch, we use advanced anti-corrosion coatings that act as a protective barrier, extending the steel’s lifespan and reducing maintenance costs in harsh environments.
We apply different types of metal coatings, each designed to offer maximum corrosion resistance:
Metallic coatings: Such as galvanizing and anodizing, which protect the steel by forming a rust-resistant layer.
Organic coatings: These include anti-corrosion paints such as epoxy and protective varnish, ideal for improving the steel’s chemical and mechanical resistance.
Plastic coatings: These provide complete insulation against moisture and corrosive agents.
Cathodic protection: An electrochemical method that prevents corrosion in metal structures exposed to extreme environments.
To ensure the effectiveness of the anti-corrosion treatment, it is essential to properly prepare the steel surface before applying the coating. At Beritch, we advise each client on the selection of the most appropriate anti-corrosion coating, ensuring optimal performance under any operating conditions.
Our coating of the steel part
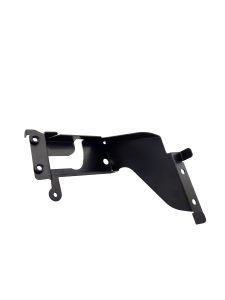
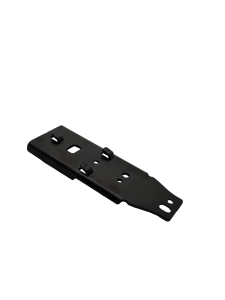
At Beritch, we are experts in steel manufacturing and treatment, allowing us to select the most appropriate anti-corrosion coatings based on the environment and conditions to which the metal parts will be exposed.
Each type of anti-corrosion coating acts as a protective barrier, preventing deterioration of stainless steel and other anti-corrosive metals against moisture, aggressive chemicals, and other corrosive agents.
Our treatments include metallic, organic, and plastic coatings, as well as cathodic protection solutions, ensuring maximum durability and resistance for each industrial application. At Beritch, we analyze each project individually to offer the most efficient anti-corrosion treatment, optimizing the performance and lifespan of the steel in any environment.
Corrosion-resistant coating
Our corrosion-inhibiting coatings are a key solution for safeguarding the durability and strength of steel under harsh conditions. Steel can progressively degrade in humid conditions, salty environments, exposure to corrosive chemicals, contact with other metals, and extreme temperatures.
Types of anticorrosive coatings for steel and metals
Anti-corrosion coatings are essential for preventing wear on steel and other metals exposed to moisture, chemicals, and harsh environmental conditions. At Beritch, we apply a variety of corrosion protection solutions, selecting the most appropriate method based on the application and environment of each part.
Stop Corrosion on Metal Surfaces
Metal coatings: galvanized and anodized
Metallic coatings protect steel by forming a corrosion-resistant layer, preventing direct contact with oxidizing agents.
Galvanizing: This involves coating steel with a layer of zinc, creating a barrier that protects against rust and abrasion. It is especially useful in structures exposed to the elements or harsh industrial environments. Anodizing: A treatment that improves corrosion resistance in metals such as aluminum, generating a protective oxide layer that also increases its durability and aesthetic appearance.
Organic coatings: anti-corrosion paint and varnish
Organic coatings create a chemical and physical barrier between the metal and corrosive agents, offering long-lasting protection.
Anticorrosive paint: Designed to prevent rust on metals such as steel and iron. Its application forms a protective film that prevents contact with oxygen and moisture. Epoxy and alkyd paint are two of the most widely used options in the industry. Anticorrosive varnish: A transparent coating that protects steel without altering its appearance. Ideal for metal parts that require a layer of anticorrosive protection without compromising their aesthetics.
Plastic coatings and cathodic protection
Plastic coatings: These are applied to the metal surface to completely isolate it from corrosive agents, offering high chemical and mechanical resistance. Cathodic protection: A system that prevents corrosion using sacrificial anodes or electrical currents, preventing rust on submerged or buried metal structures, such as pipelines and vessels.
Anti-rust treatments for steel and other metals
In addition to coatings, there are antioxidant treatments that neutralize and prevent corrosion, even when it has already begun to affect the metal surface.
Rust Passivator: How to Stop Corrosion
Once rust has begun to form, it’s essential to halt its progress with a rust passivator. At Beritch, we use passivating chemicals that react with the rust present on steel or iron, transforming it into a harmless substance and stabilizing the surface to prevent its spread.
Anti-corrosive paint and anti-corrosive varnish
For preventative corrosion protection, we apply high-resistance anti-corrosion paints and varnishes.
- Anti-corrosion paint creates a protective barrier on the metal surface, insulating it from moisture, chemicals, and extreme environmental conditions.
- Anti-corrosion varnish provides a transparent layer that reinforces the steel’s strength without altering its appearance, ideal for applications where protection is required without altering aesthetics.
Both coatings extend the steel’s lifespan and improve its mechanical resistance to wear and abrasion.
Anticorrosive for metal and preventive maintenance
The use of anticorrosives for metals is an effective solution to prevent the deterioration of metal structures. These products are applied directly to the steel surface, forming a protective layer that prevents the action of corrosive agents.
To maximize their effectiveness, it is recommended to combine them with preventive maintenance, which includes periodic inspections and the reapplication of protective coatings in areas exposed to aggressive conditions.
At Beritch, we advise our clients on the selection of the most appropriate anti-corrosion treatment, ensuring optimal protection and greater durability of metal structures in any environment.
FAQs
How to prevent stainless steel from rusting?
Although stainless steel is highly resistant to corrosion, it is not completely immune. To prevent rust, it is recommended to:
- Keep the surface clean and free of contaminants.
- Avoid contact with less noble metals that can cause galvanic corrosion.
- Apply an additional anti-corrosion coating in highly aggressive environments.
- Use specific cleaning products that do not damage the stainless steel’s passive layer.
What can rust stainless steel?
Stainless steel can rust if exposed to certain adverse factors, such as:
- Saline environments: The high concentration of chlorides in the air, especially in coastal areas, can accelerate corrosion.
- Prolonged exposure to aggressive chemicals, such as strong acids and industrial chlorides.
- High temperatures, which can alter the chemical composition of the steel and weaken its resistance to rust.
- Contact with other metals, which can cause corrosion due to cross-contamination or galvanic corrosion.
Which steel is most resistant to corrosion?
Austenitic stainless steel, especially grades 316 and 904L, is known for its high corrosion resistance, even in extremely aggressive environments. These alloys contain a higher percentage of chromium, nickel, and molybdenum, making them ideal for applications in the marine, chemical, and food industries.
Which anti-corrosion coating is best for steel?
The choice of anticorrosive coating depends on the environment and the application of the steel. Among the most effective options are:
- Galvanized: Ideal for structures exposed to the elements.
- Anticorrosive paint: Recommended for parts subject to abrasion or chemical agents.
- Anodized: Perfect for improving the strength of aluminum and other light metals.
- Cathodic protection: Used on pipelines and submerged structures to prevent rust.
How does anti-corrosion paint work on metal?
Anti-corrosion paint for metal acts as a protective barrier that prevents the steel from coming into contact with oxygen and moisture. When applied correctly to a clean surface, it prevents rust formation and prolongs the material’s lifespan.
What is the difference between a coating and an anti-corrosion treatment?
- Anticorrosive coating: This coating is applied to the surface of the steel to insulate it from external agents. It can be a layer of paint, varnish, or a metallic material such as zinc.
- Anticorrosive treatment: This includes chemical or physical processes that modify the structure of the metal to improve its resistance to corrosion, such as rust passivation or preventive maintenance.
What materials are anticorrosive and which one should you choose?
There are various anti-corrosion materials designed to protect steel and other metals:
- Anti-corrosion metals: Stainless steel, anodized aluminum, titanium.
- Anti-corrosion coatings: Epoxy paint, protective varnish, hot-dip galvanizing.
- Anti-rust treatments: Rust passivators and cathodic protection.
The best option will depend on the type of exposure the metal will be subjected to and its specific use.
Bericht Projects
- All
- Operation stamping
- Progressive stamping
- Welded insert assemblies
- Welded assemblies
- Assembled assemblies
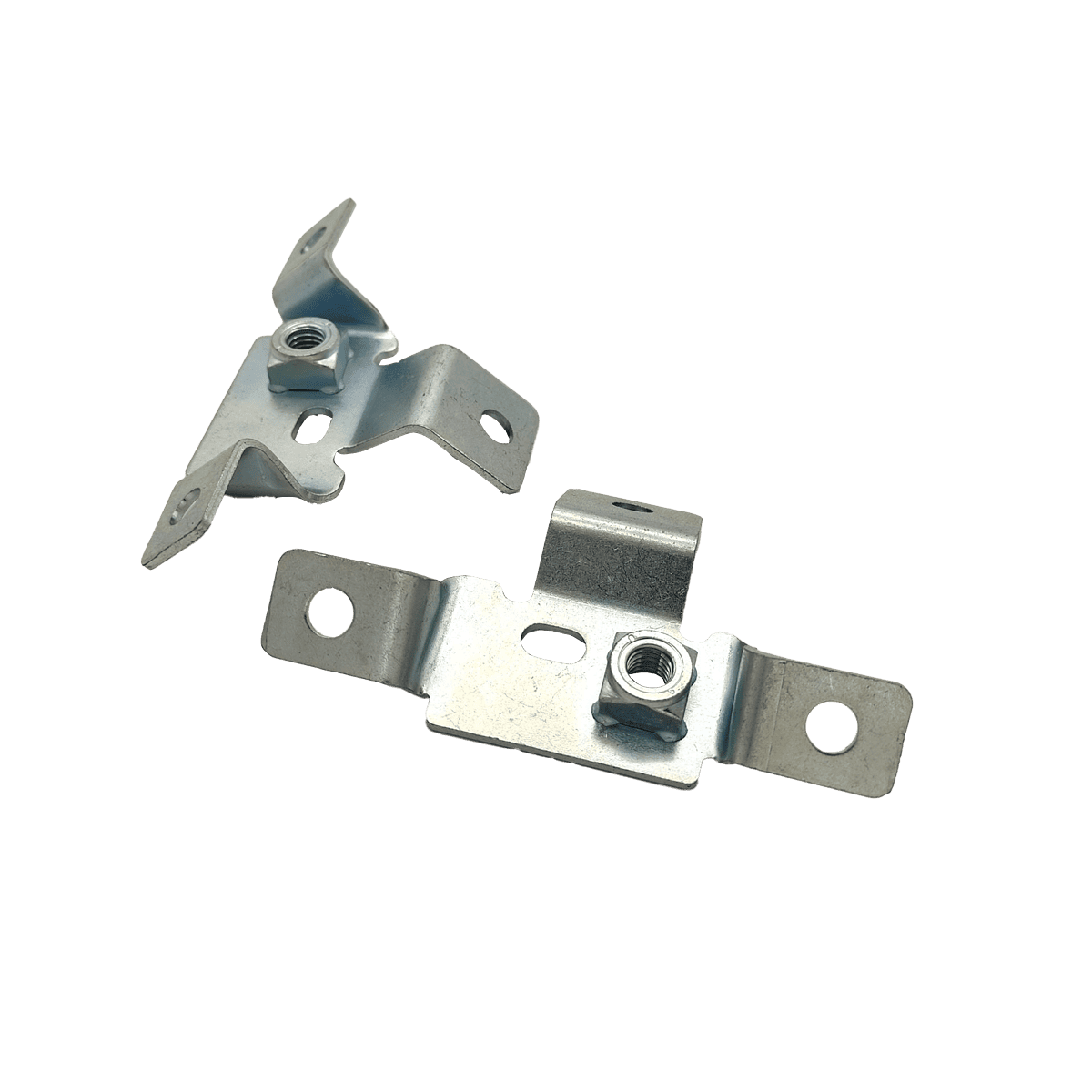
OEM: Volkswagen
Thickness: 4 mm
Annual production: 7.400
Surface treatment: Zinc
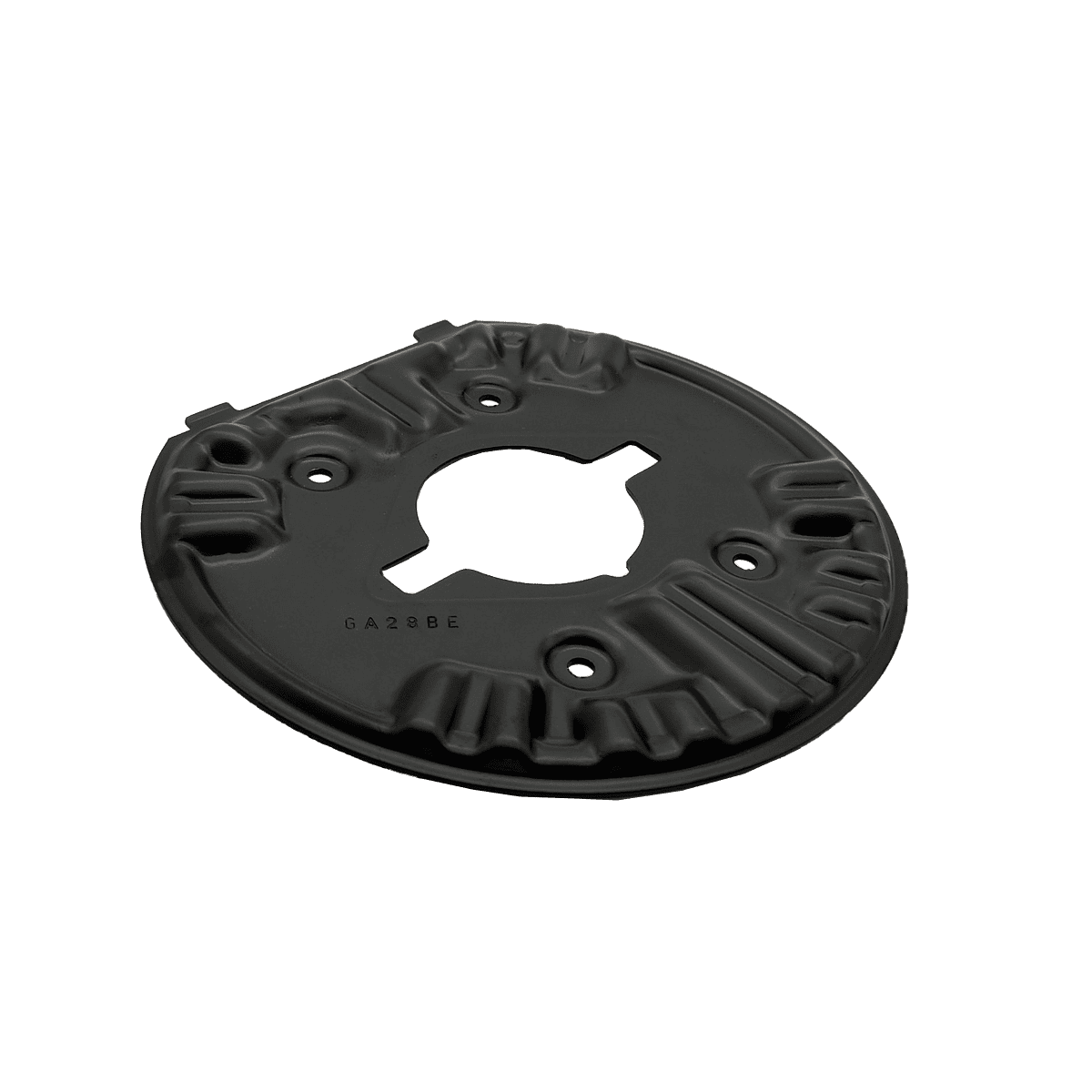
OEM: PSA
Material: DC01
Thickness: 1,5 mm
Anual production: 200.000
Surface treatment: Cataphoresis
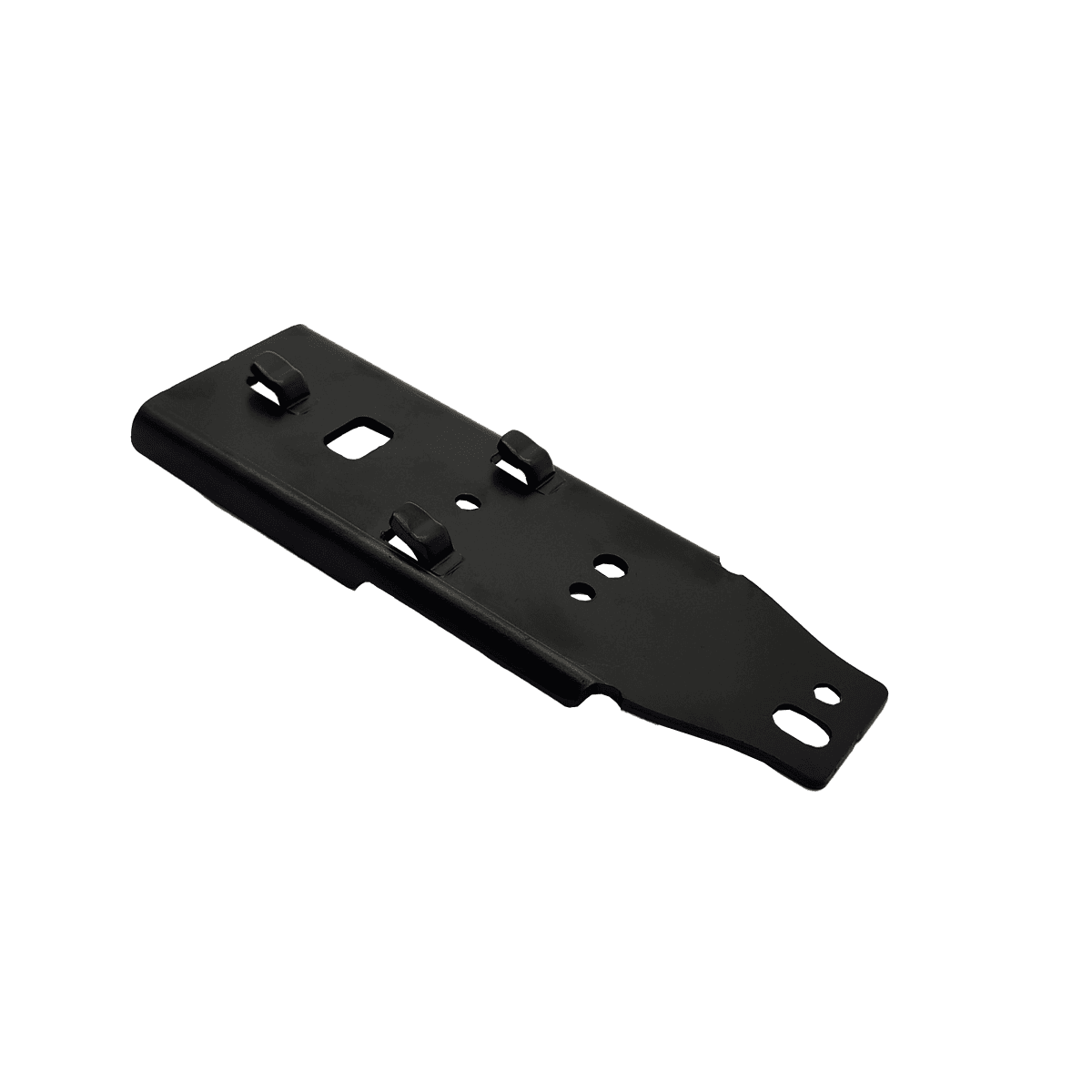
OEM: Renault
Material: DD13
Thickness: 3 mm
Annual production: 150.000
Surface treatment: Cataphoresis
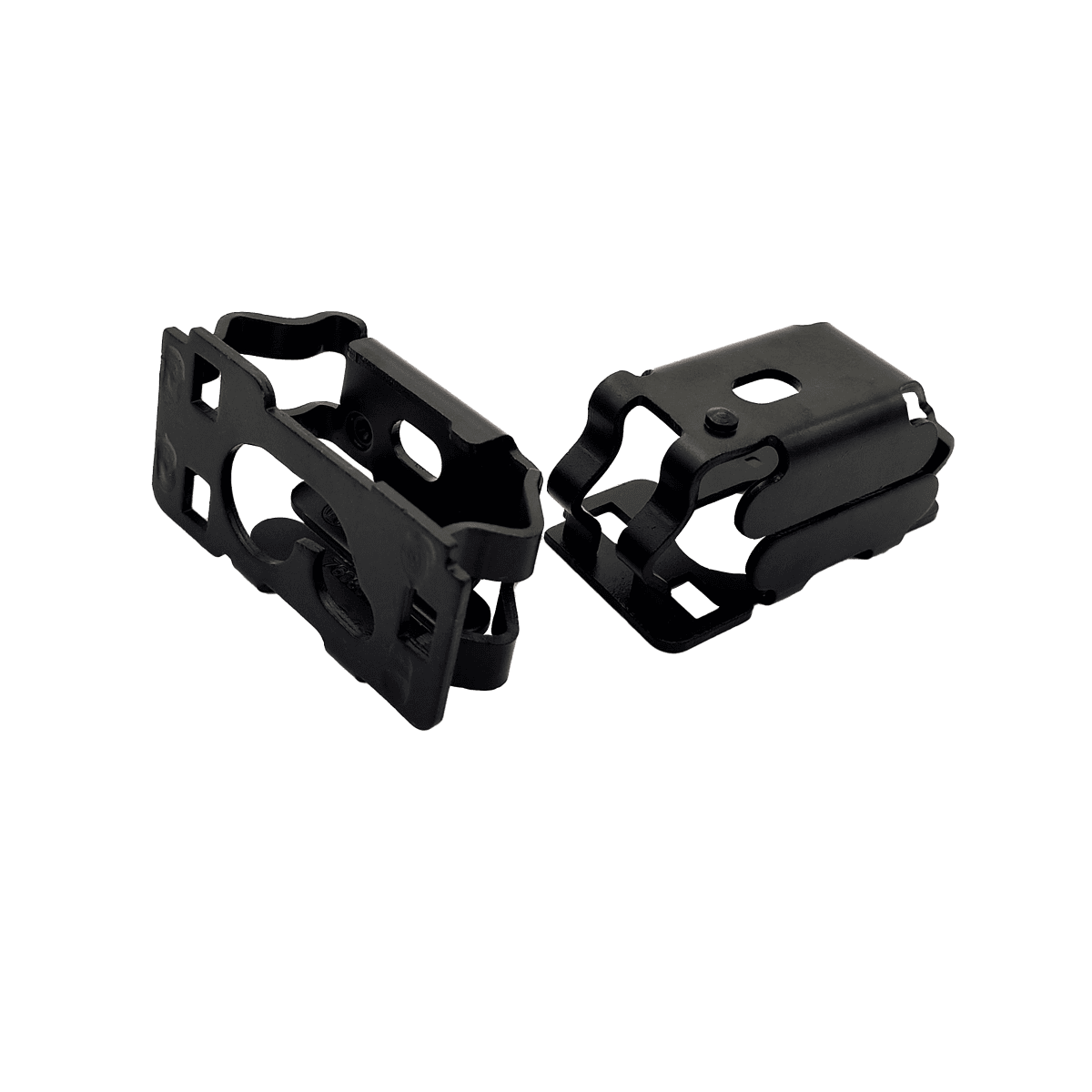
OEM: Volkswagen
Material: S420MC
Thickness: 2,5 mm
Annual production: 14.800
Surface treatment: Cataphoresis
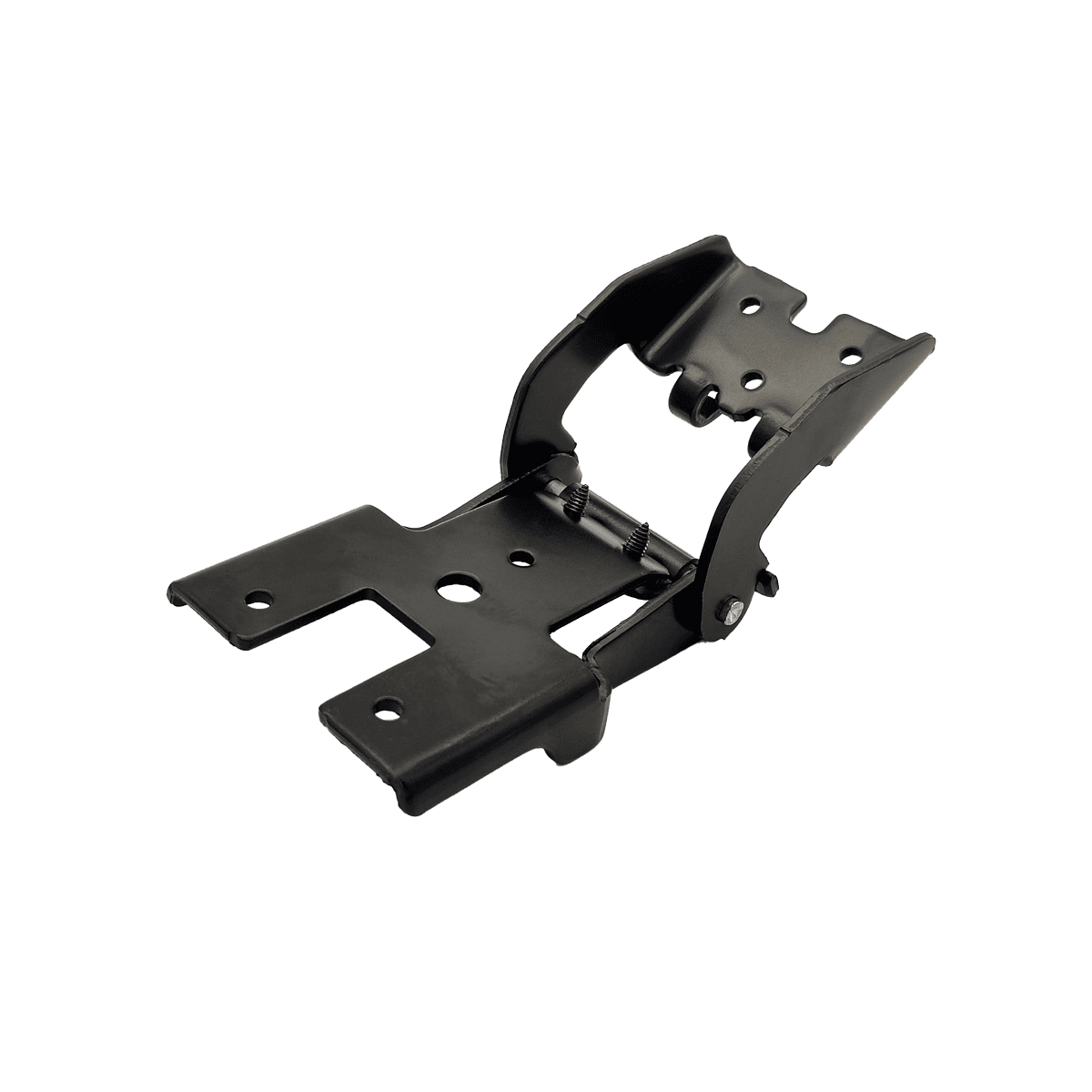
OEM: Renault
Material: DD13
Thickness: 3 mm
Annual production: 100.000
Surface treatment: Cataphoresis
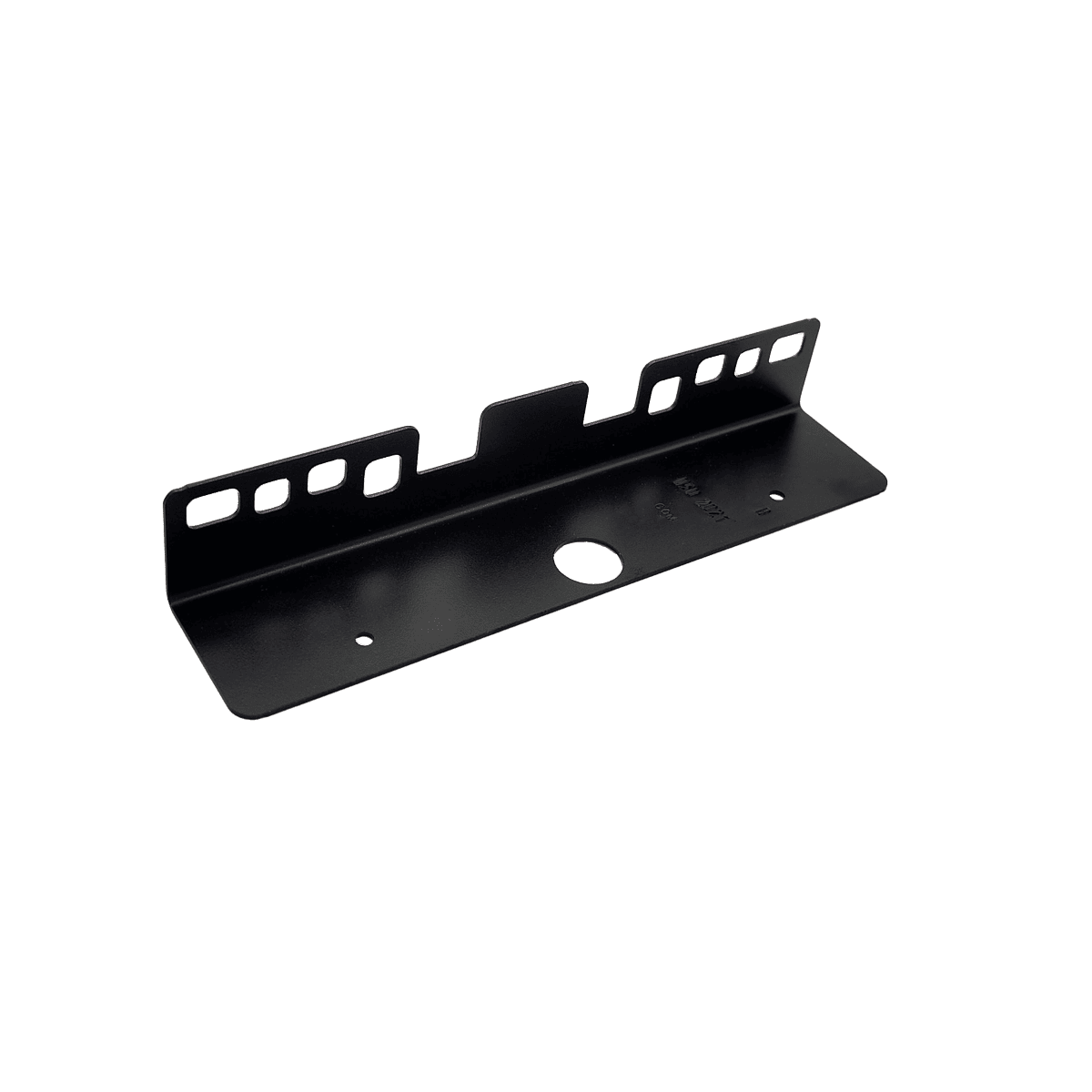
OEM: Renault
Material: HC42LA
Thickness: 1 mm
Annual production: 200.000
Surface treatment: Cataphoresis
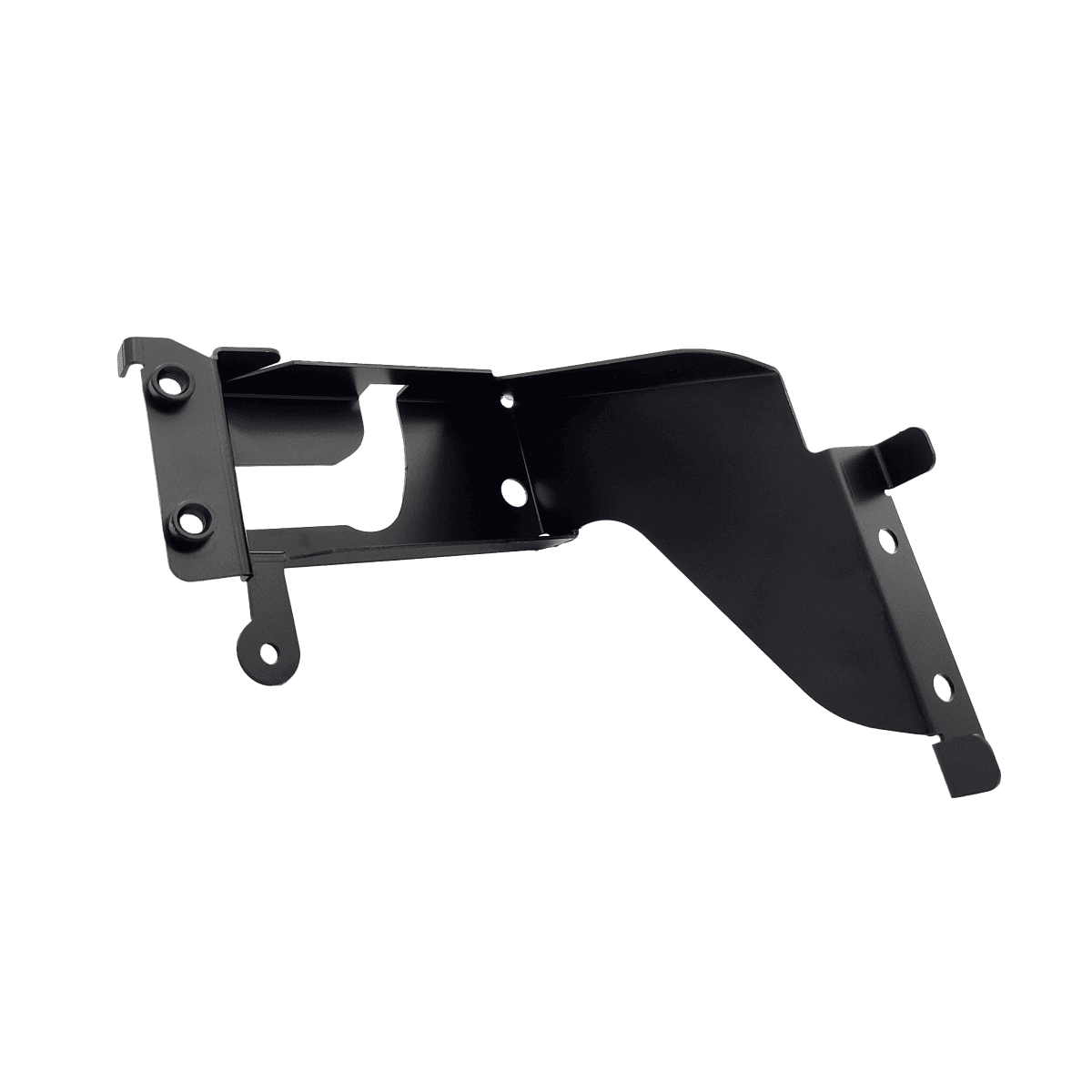
OEM: Renault trucks
Material: S420MC
Thickness: 1,5 mm
Annual production: 1.800
Surface treatment: Cataphoresis
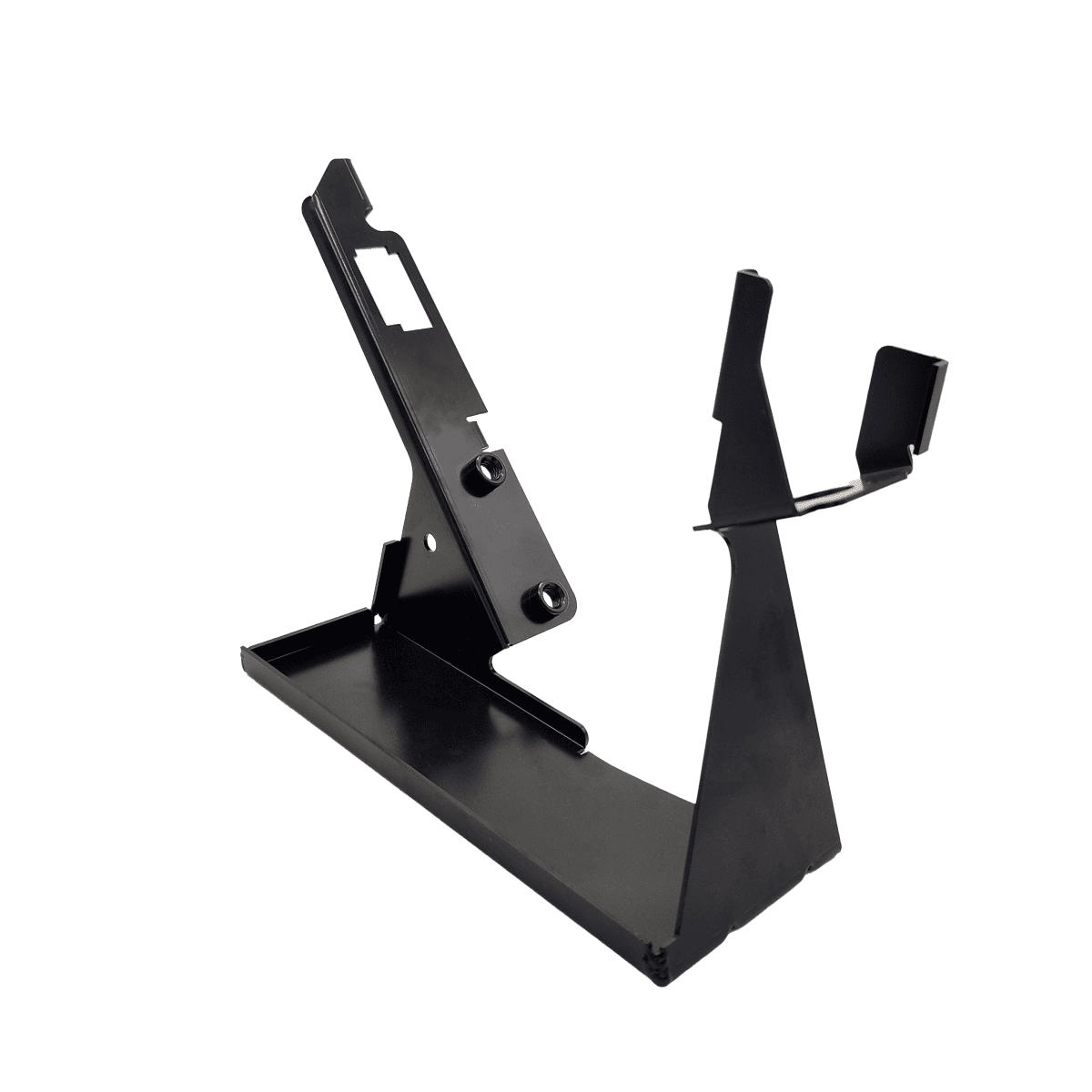
OEM: Renault trucks
Material: S420MC
Thickness: 1,5 mm
Annual production: 1.800
Surface treatment: Cataphoresis
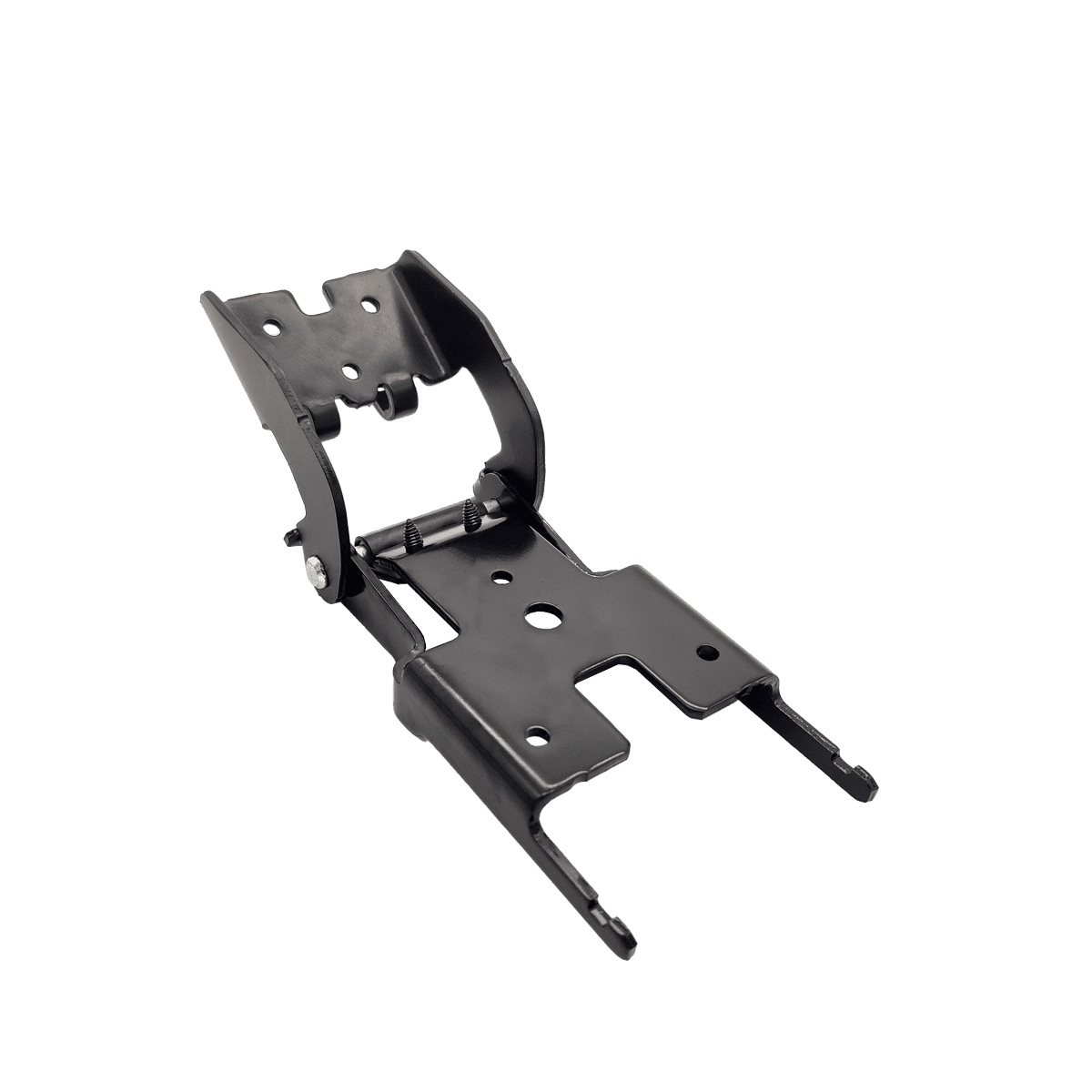
OEM: Renault
Material: DD13
Thickness: 3 mm
Annual production: 150.000
Surface treatment: Cataphoresis
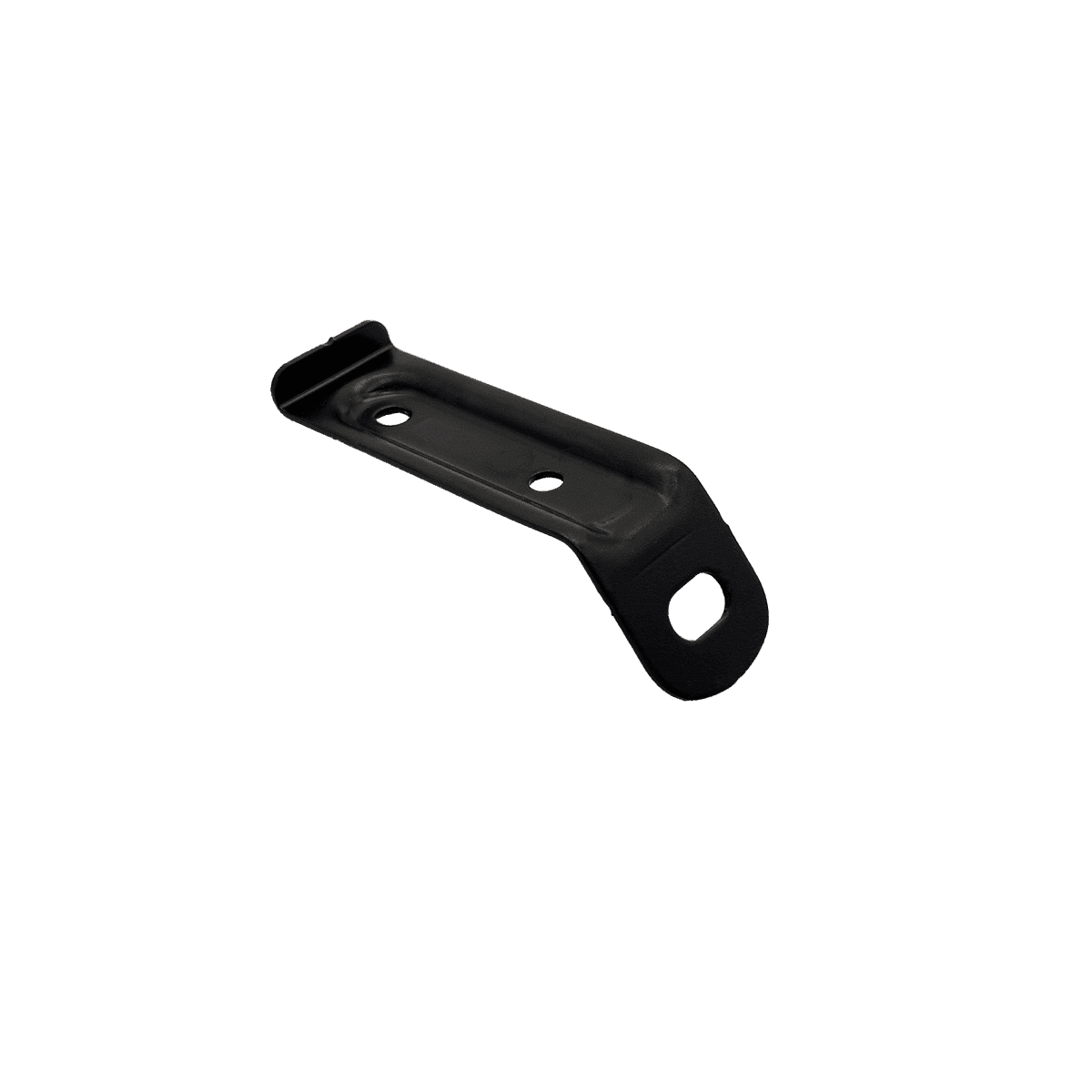
OEM: Daimler
Material: HC380LA
Thickness: 1,5 mm
Annual production: 200.000
Surface treatment: Cataphoresis
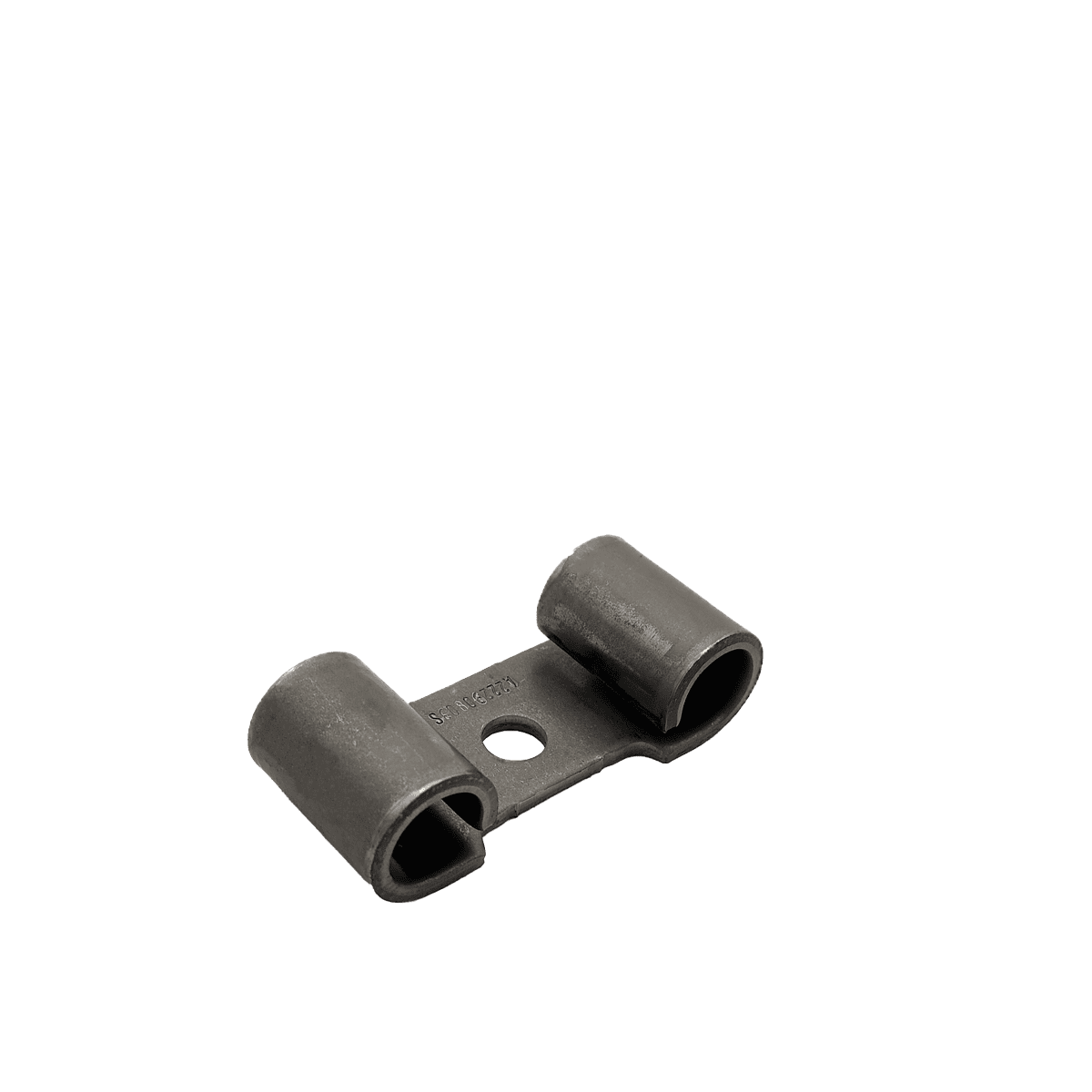
OEM: Volkswagen
Material: S355MC
Thickness: 4mm
Annual production: 1.100.000
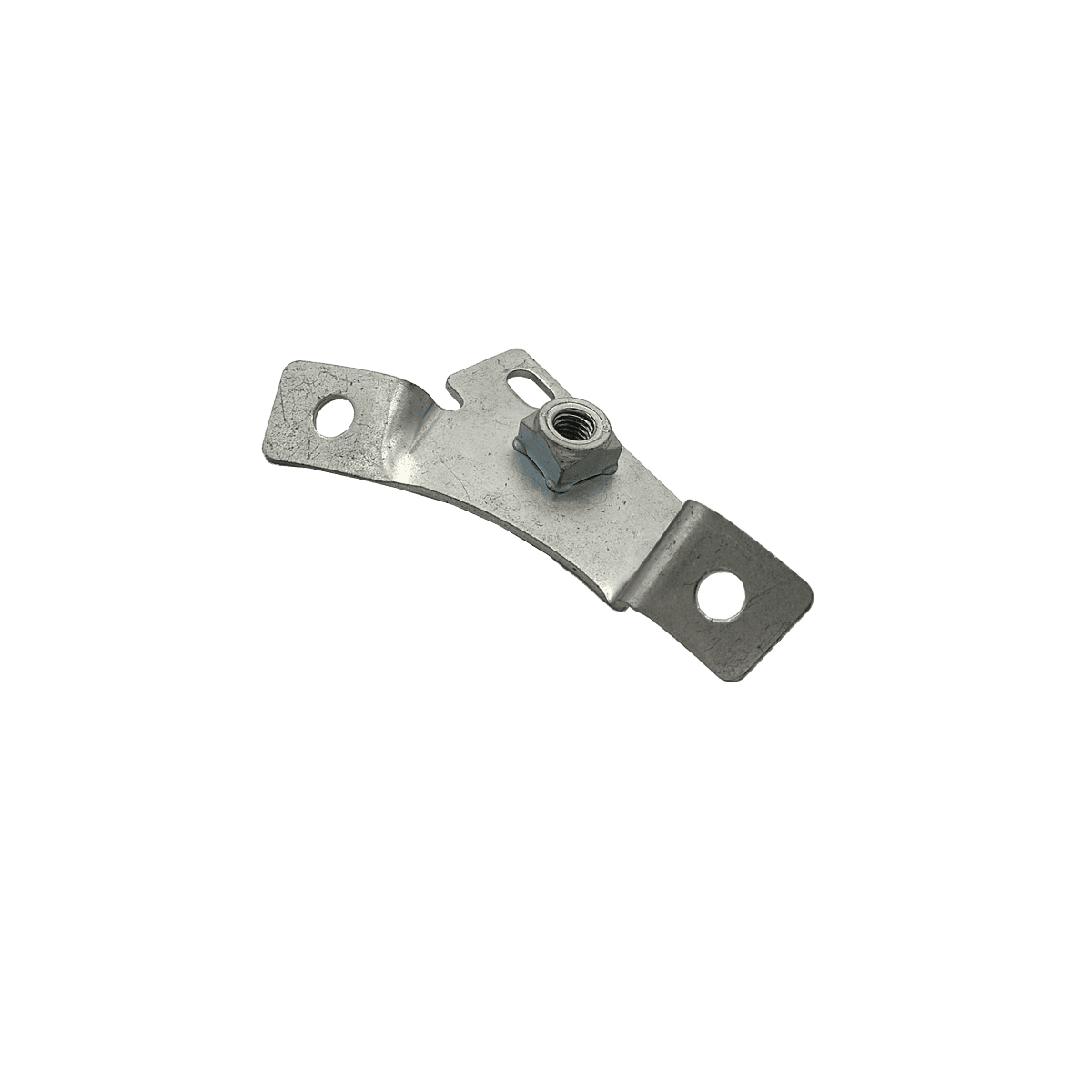
OEM: Volkswagen
Material: S420MC
Thickness: 2 mm
Annual production: 7.400
Surface treatment: Zinc
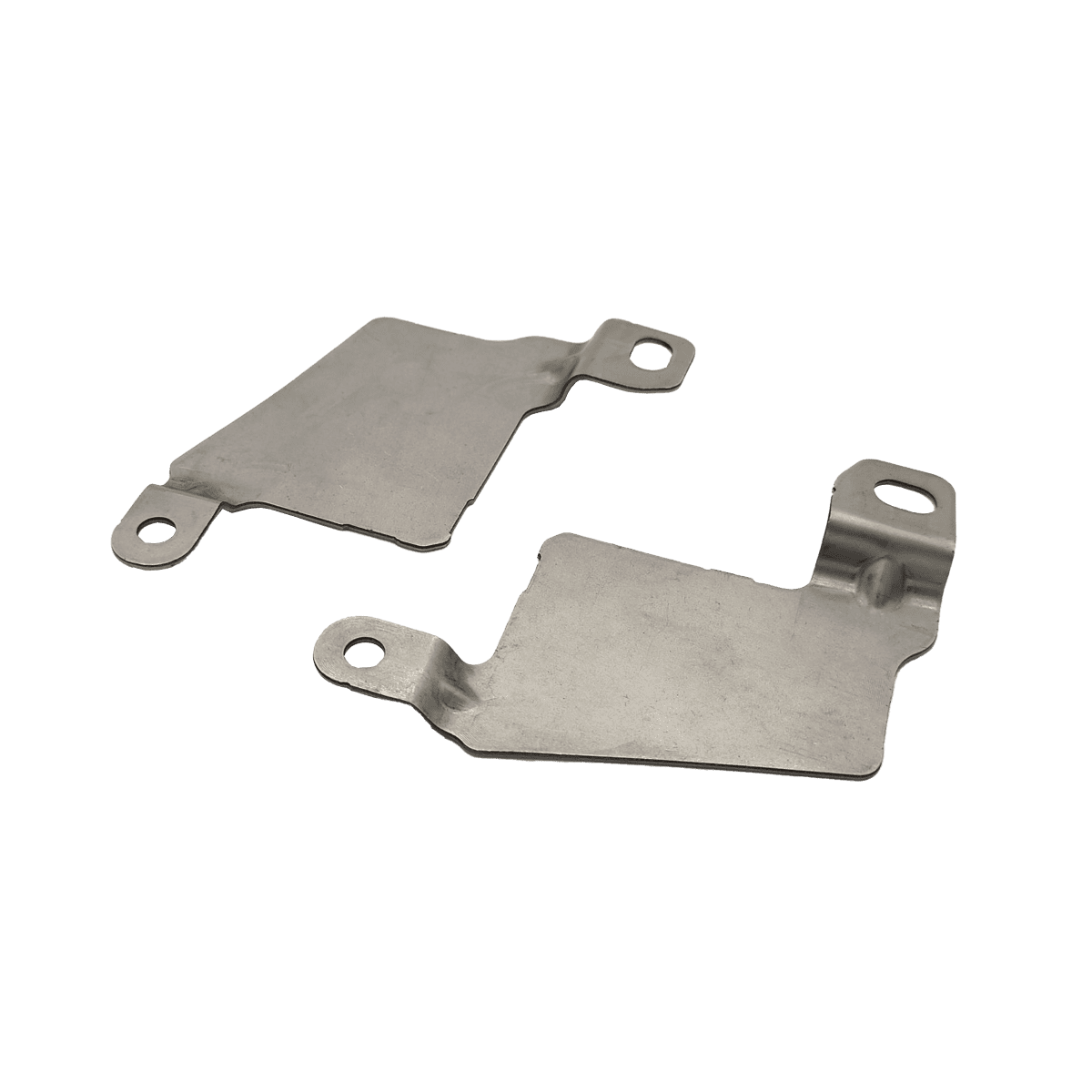
OEM: Volkswagen
Material: CR380LA
Thickness: 1,5 mm
Annual production: 300.000 (1+1)
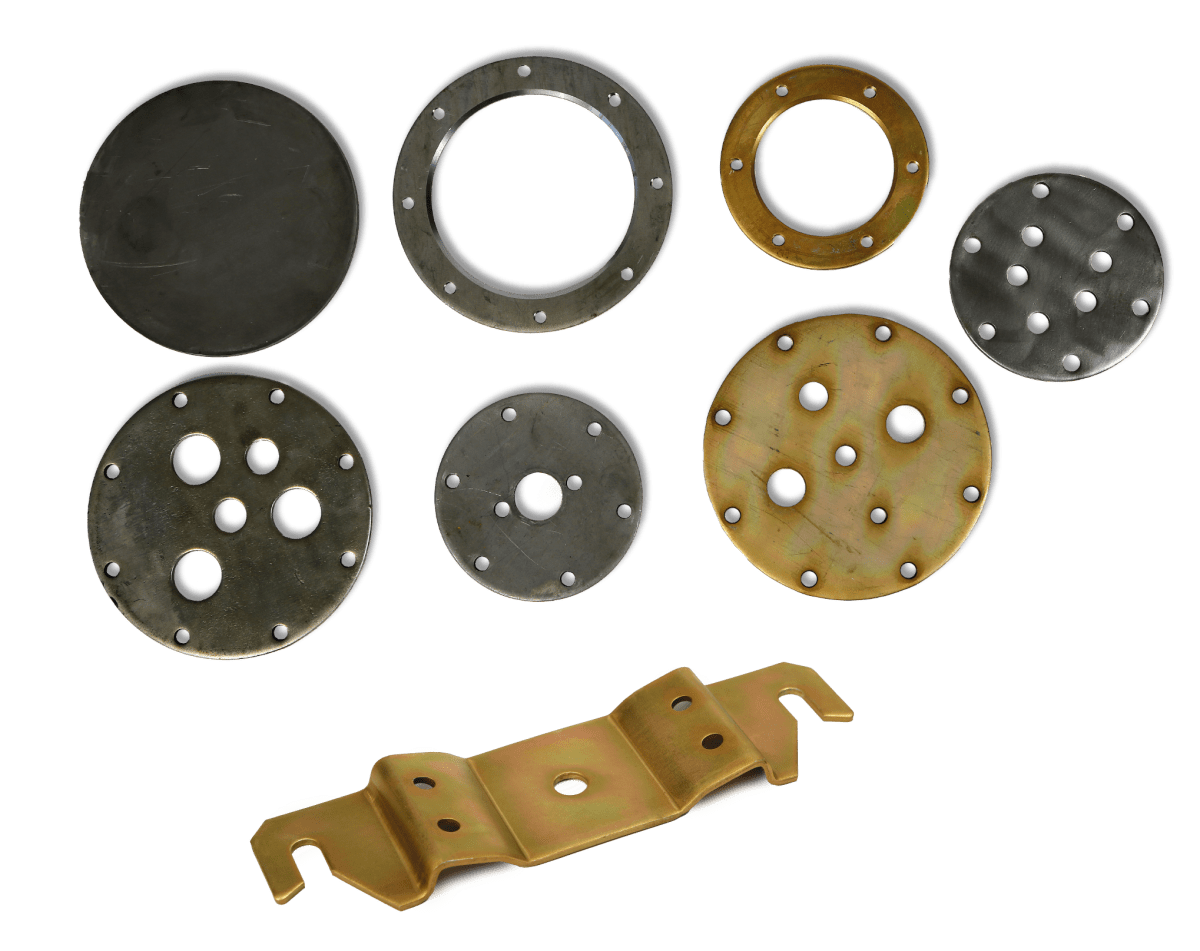
SIPEJMA
Material: Varios (S275JR, St 33, S185, P355N)
Thickness: 3 / 8 mm
Annual production: varios
Surface treatment: Zinc
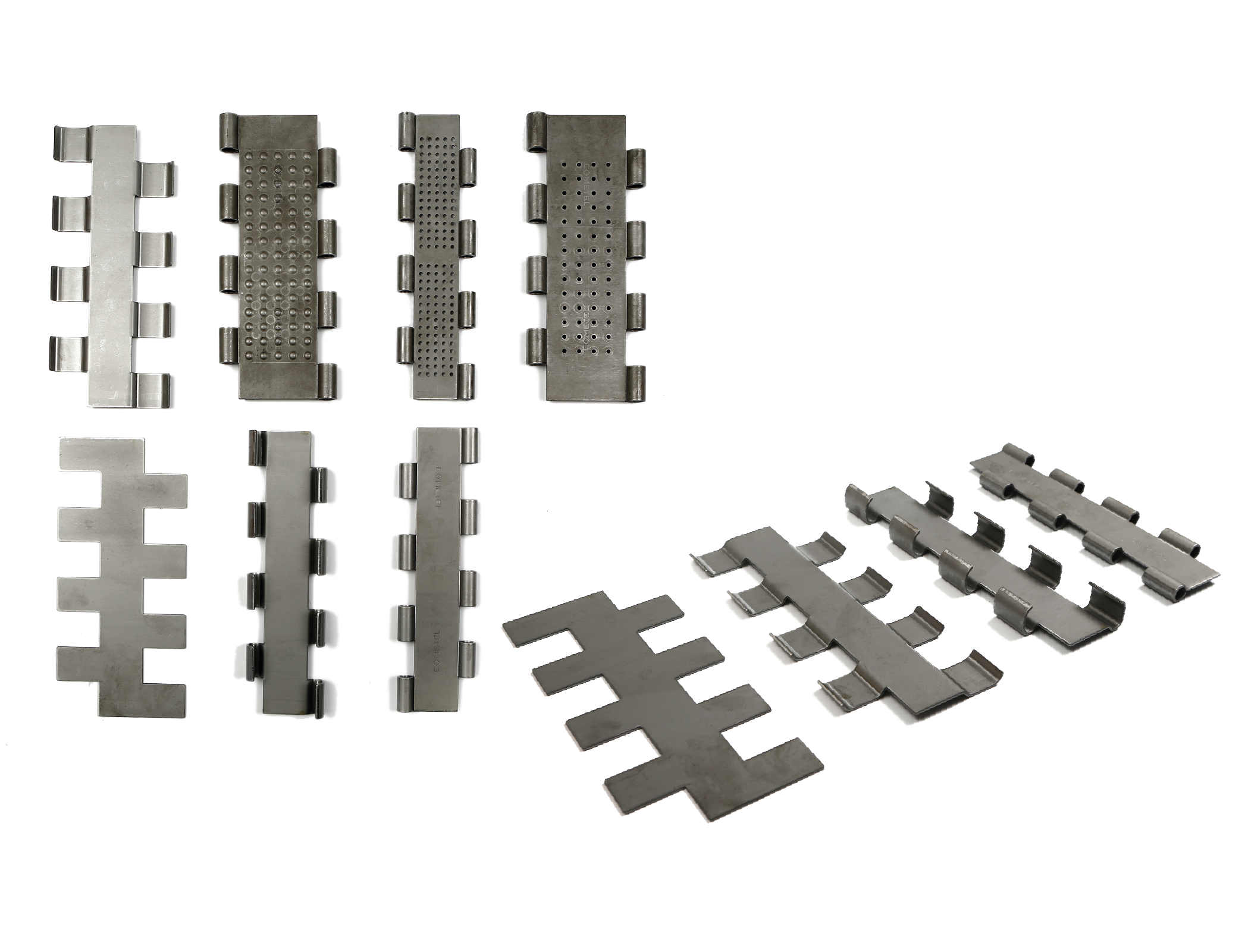
COMETEL
Material: Various (S275JR, DD11)
Thickness: 2 / 6 mm
Annual production: Various
Surface treatment: N/A
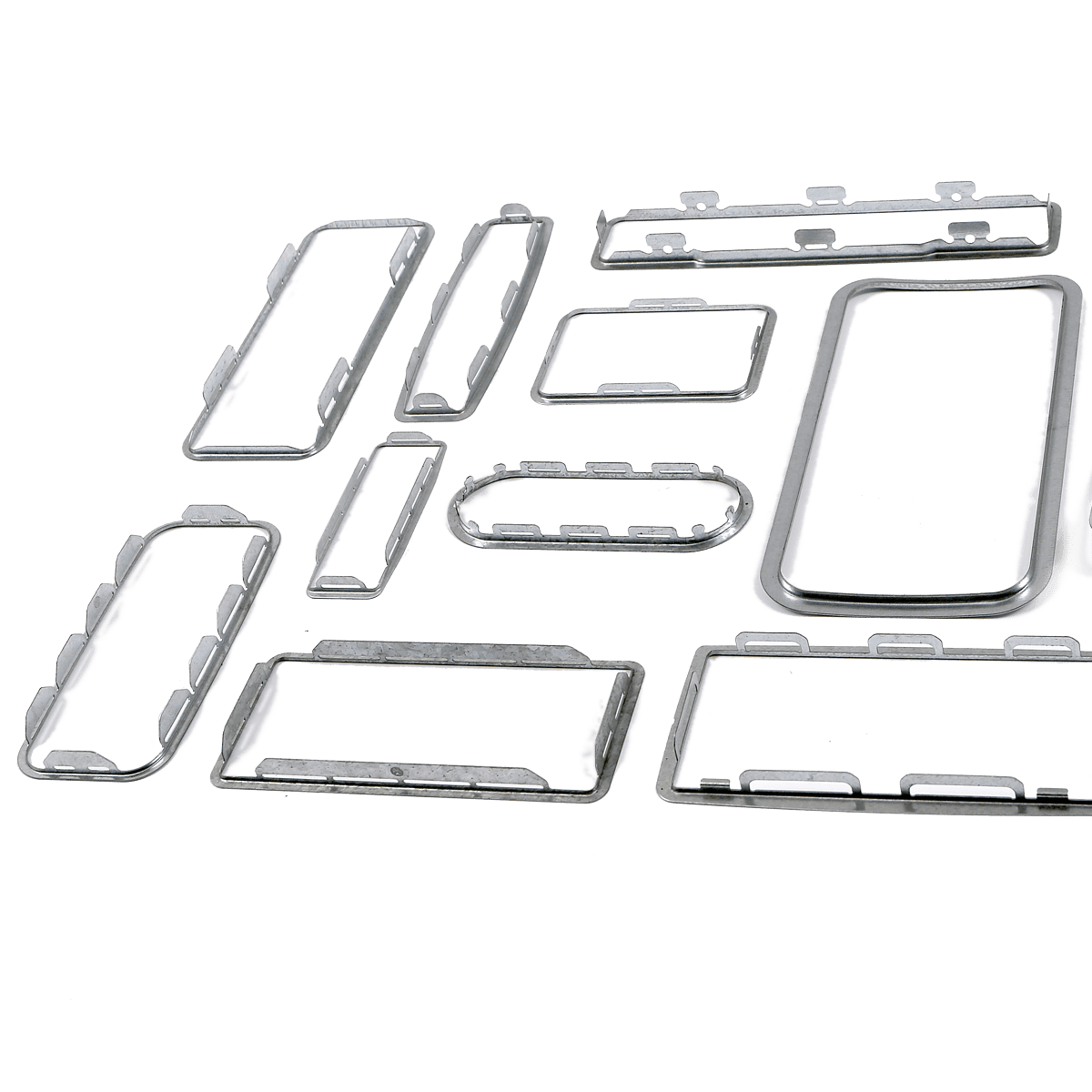
OEM: Ford, Volkswagen, Audi...
Material: Various (DX51D, DX52D)
Thickness: 0,5 / 0,7 mm
Annual production: Various
Surface treatment: Zinc
Discover our Advanced Metal Stamping Solutions
At Beritch, we are specialists in the manufacturing of metal parts using stamping, welding, coating and assembly processes. Our extensive industry experience allows us to offer customized solutions for sectors such as automotive, naval, aeronautical, and petrochemical, guaranteeing the maximum quality and precision in every product.
Our solutions include:
- Progressive and phased stamping: Advanced technology for the mass production of metal parts with maximum efficiency.
- Painting and anti-corrosion coating processes: We apply anti-corrosion paint for metal, varnishes, and other anti-corrosion treatments to increase the strength and durability of steel.
- Welding and assembly: We manufacture welded and assembled assemblies that meet the highest safety and quality standards.
- Part design and development Metal parts: We advise our clients on the creation of components tailored to their specific needs.
If you are looking for a reliable supplier of stamped metal parts with high-performance anti-corrosion coatings, at Beritch we offer innovative solutions tailored to each industry.