What is MIG welding?
MIG-MAG welding, also known as wire welding because it uses a wire as an electrode, is a high-speed welding process widely used in various industrial sectors, but especially in the metallurgical industry.
This term actually includes two variants of the same type of welding: MIG welding and MAG welding. At Beritch, we perform both processes to offer a high-precision industrial welding service.
How does MIG/MAG welding work?
MIG MAG welding works by creating an electric arc between the wire electrode, made of a material similar to the base metal, and the workpiece. During the process, intense heat is generated, causing the metals to fuse and forming a weld bead.
A shielding gas is used to protect the weld bead from atmospheric contamination. MIG welding uses a different gas than MAG welding.
What is the difference between MIG and MAG welding?
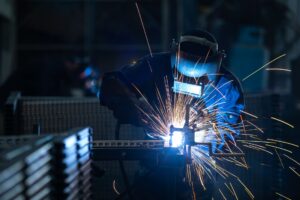
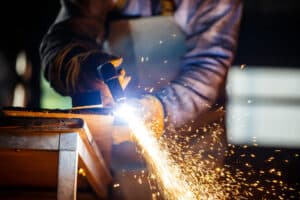
The main difference between MIG and MAG welding is the type of shielding gas used.
MIG welding uses an inert gas, while MAG welding uses an active gas or a gas mixture. This influences the properties of the weld bead, as the shielding gas can affect arc stability and the transfer characteristics of the filler metal. The use of active gases in MAG welding, on the other hand, results in greater slag release. This type of welding is used to join carbon and low-alloy steels.
On the other hand, MIG welding is considered more suitable for welding non-ferrous materials, such as aluminum and copper.
Structure of a MIG/MAG welding system
The structure of the MIG/MAG welding system is composed of several important components, essential for performing the welding process.
- Power source: Supplies the electric current necessary to create the welding arc.
- Welding gun: Used to guide the wire electrode and supply the shielding gas.
- Wire feeder: Continuously feeds the wire electrode through the welding gun.
- Grounding cable: Essential for ensuring the welder’s safety.
Types of MIG/MAG welding processes
There are different types of MIG/MAG welding processes used depending on the needs of each application.
MIG/MAG welding processes
Semi-automatic process
In the semi-automatic process, the welder manually guides the welding gun, controlling the speed and direction of the weld bead. The wire feed system and gas supply are automatic, which facilitates the welder's task.
Automatic process
In the automatic process, the welding gun is mounted on a computer-controlled tracking mechanism. The movement of the gun and the adjustment of the various welding parameters are automated, ensuring greater precision.
Robotic process
In the robotic process, welding is performed using an industrial robot programmed to perform precise and controlled movements. This type of process is highly efficient and is used in high-production applications, such as automotive factories, where a high-quality welding process requires repeated repetition.
What gases are used for MIG/MAG welding?
In MIG and MAG welding, different shielding gases are used for each variant depending on the material being welded. The most commonly used gases are:
Argon
It is mainly used in MIG welding, but also in MAG.
Helium
It is used in MIG welding and is sometimes combined with argon.
Carbon dioxide (CO2)
It is used in MAG welding
Combination of argon and carbon dioxide
They are used in MAG welding.
Advantages and disadvantages of MIG/MAG welding
Advantages of MIG/MAG welding
This technique offers several significant advantages over other welding methods. Some of the key advantages include:
Disadvantages of MIG/MAG welding
MIG MAG welding also has some disadvantages to consider:
- High speed. Compared to other types of welding, it has a high deposition capacity.
- Clean, high-quality welding. The use of shielding gas results in less slag production and improves joint quality.
- Ease of use. MIG/MAG welding is relatively easy to learn and use.
- Versatility. It can be used to weld many types of metals.
- Less distortion and warping. Thanks to high speed and heat control, the part is less warped.
- Sensitivity to surface quality. MIG/MAG welding is sensitive to the presence of rust, paint, grease, and other contaminants on the surface of the material to be welded, so the surface must be prepared first.
- Higher cost. The equipment is more expensive than other types of welding, in addition to the wire and gas consumption.
- Limitations. It is not suitable for all types of metals, being too weak for some and too strong for others.
What can be welded with MIG MAG?
MIG/MAG welding is versatile and can be used to weld a wide variety of metals, including carbon steel, stainless steel, aluminum, copper, nickel, and their alloys.
This type of welding is suitable for welding thin or medium-thick materials and is high-speed.
¿Dónde se usa la soldadura MIG MAG?
This type of welding is used in various industrial sectors due to its great versatility, quality, and speed.
It is used in the automotive industry, machinery manufacturing, metal structures, pressure vessels, and the repair and maintenance of metal equipment and structures, among many other applications.
MIG MAG welding parameter table
The MIG/MAG welding parameter table provides a general guide for setting the appropriate parameters, such as current, voltage, wire feed speed, and shielding gas type.
Welding parameters can vary depending on several factors, including material type, metal thickness, welding position, and welder skill.
MIG MAG welding is considered easier to learn and use compared to other types of welding, such as TIG welding.
MIG MAG welding offers several advantages, such as high welding speed, clean, high-quality welds, ease of use, versatility in welding different metals, and reduced distortion and deformation of welded parts.
MIG welding is a variant of the MIG/MAG welding process that uses an inert gas, such as argon or helium, as a shielding gas. It is primarily used for welding non-ferrous materials, such as aluminum and copper.
In addition to being performed differently, TIG welding is more precise, slower and more difficult to perform than MIG.
To perform MIG welding, you need a power source, a welding gun with a wire feeder, a shielding gas, welding wire, and welding parameters set correctly according to the material type and thickness.
MIG welding is best for quick welds, while electric welding may be better suited for smaller, more precise jobs.
MAG (Metal Active Gas) welding uses an active gas instead of an inert one.
Carbon and low alloy steels, stainless steel, copper and nickel, depending on the requirements and the shielding gas used.
The acronym MIG stands for Metal Inert Gas, while MAG stands for Metal Active Gas.
The acronym MIG stands for Metal Inert Gas, while MAG stands for Metal Active Gas.
TIG welding is used for jobs that require high quality, precision, and manual control. MIG welding is best for jobs that require speed and productivity.
The main difference between MIG MAG and TIG welding lies in the type of electrode used, the shielding gas and the welding process.
In general, TIG welding is considered stronger than MIG/MAG welding when considering strength, although this will depend on the material and other factors.
The main difference between gas and gasless MIG welding is the type of electrode used. In gas MIG welding, a solid wire electrode is continuously fed through the welding gun.
In gasless MIG welding, a flux-cored wire electrode is used, which produces a shielding gas when molten. This type of welding is generally of lower quality.
- All
- Operation stamping
- Progressive stamping
- Welded insert assemblies
- Welded assemblies
- Assembled assemblies
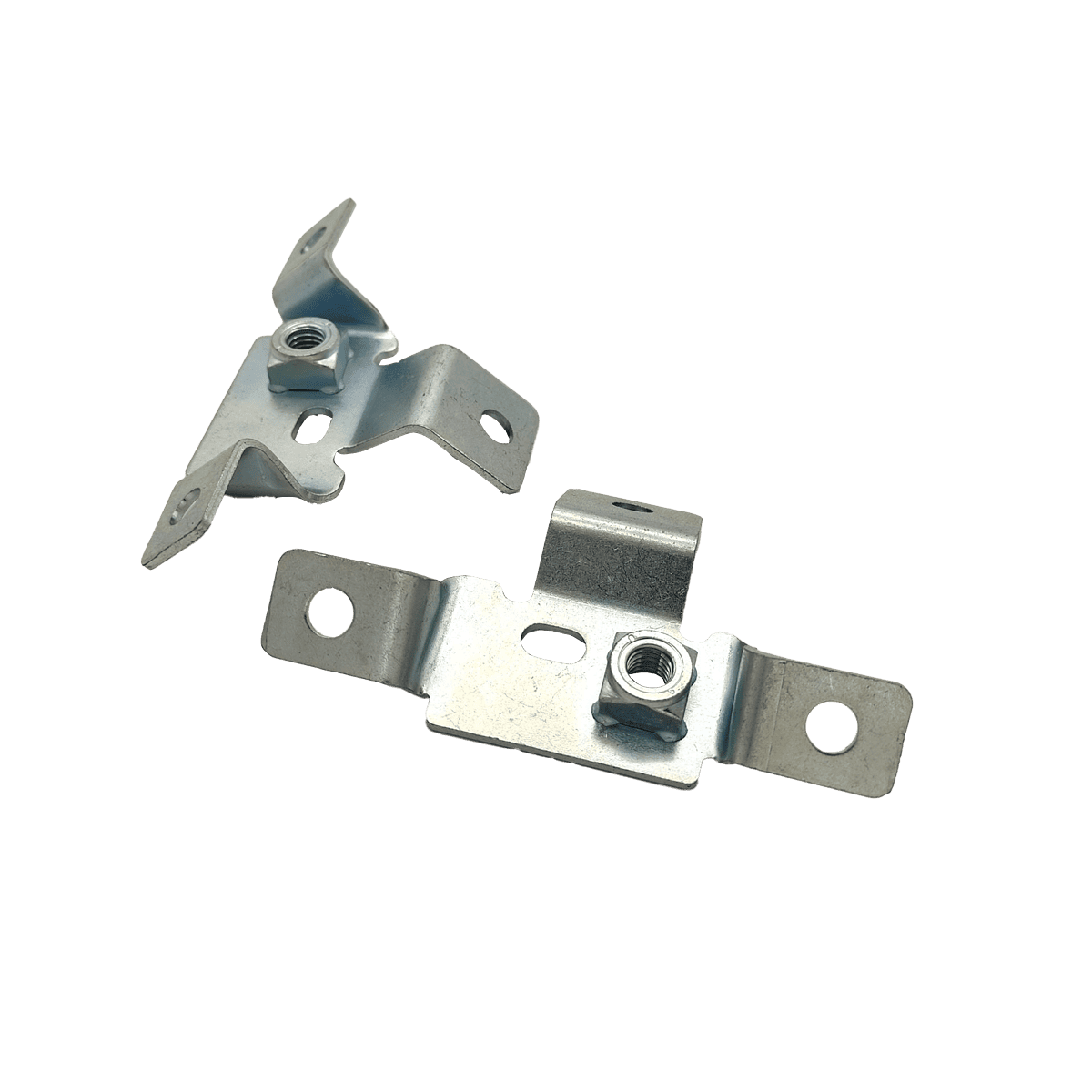
OEM: Volkswagen
Thickness: 4 mm
Annual production: 7.400
Surface treatment: Zinc
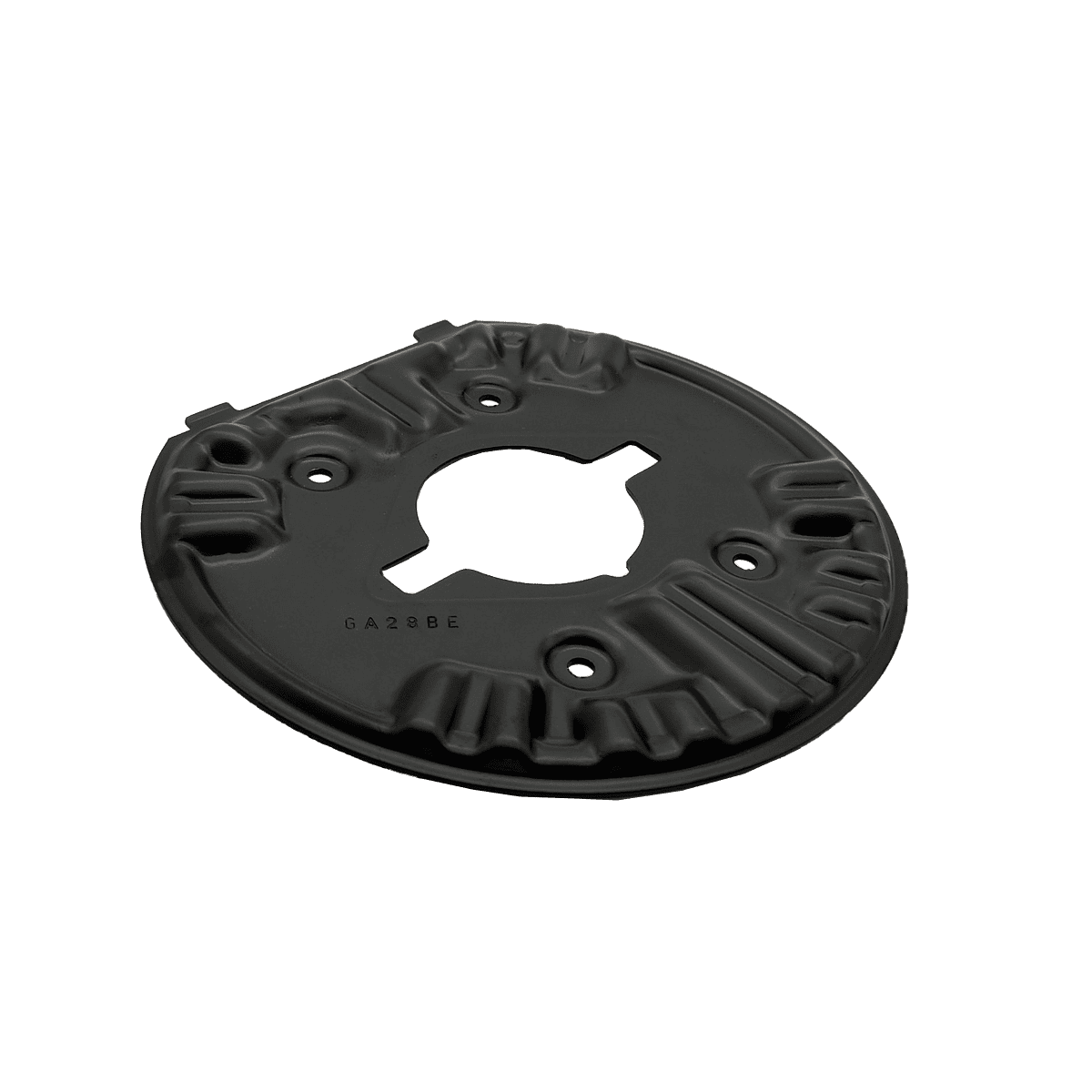
OEM: PSA
Material: DC01
Thickness: 1,5 mm
Anual production: 200.000
Surface treatment: Cataphoresis
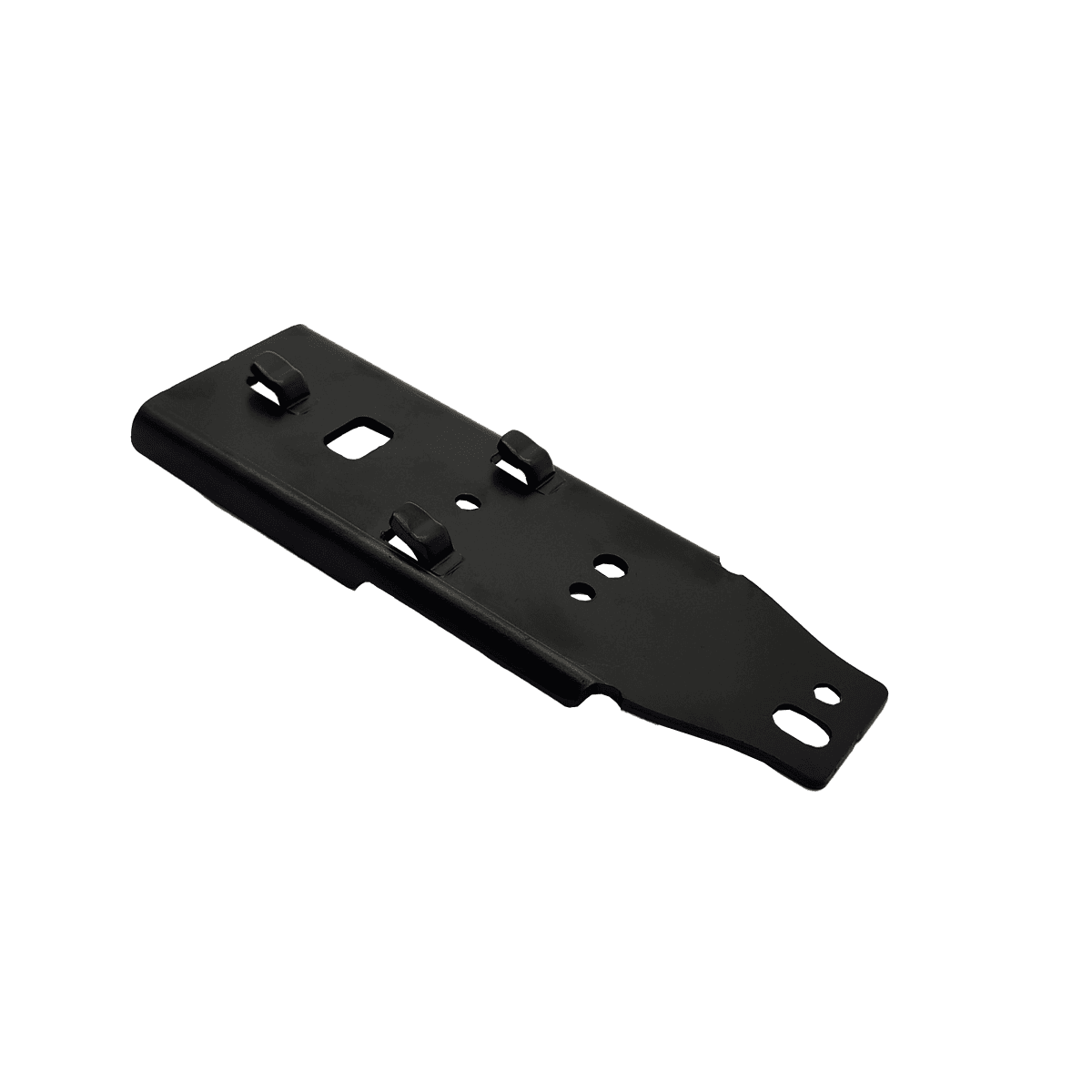
OEM: Renault
Material: DD13
Thickness: 3 mm
Annual production: 150.000
Surface treatment: Cataphoresis
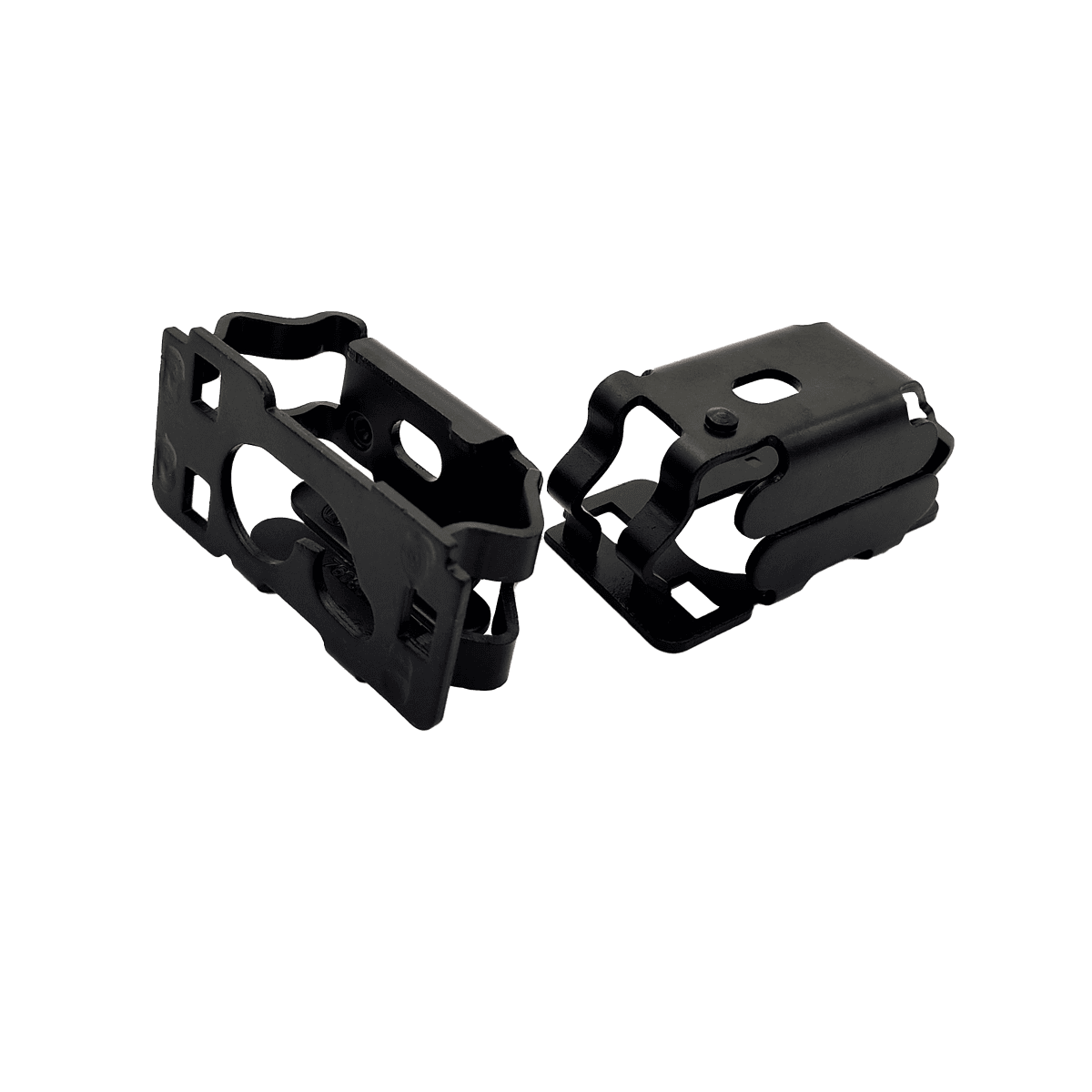
OEM: Volkswagen
Material: S420MC
Thickness: 2,5 mm
Annual production: 14.800
Surface treatment: Cataphoresis
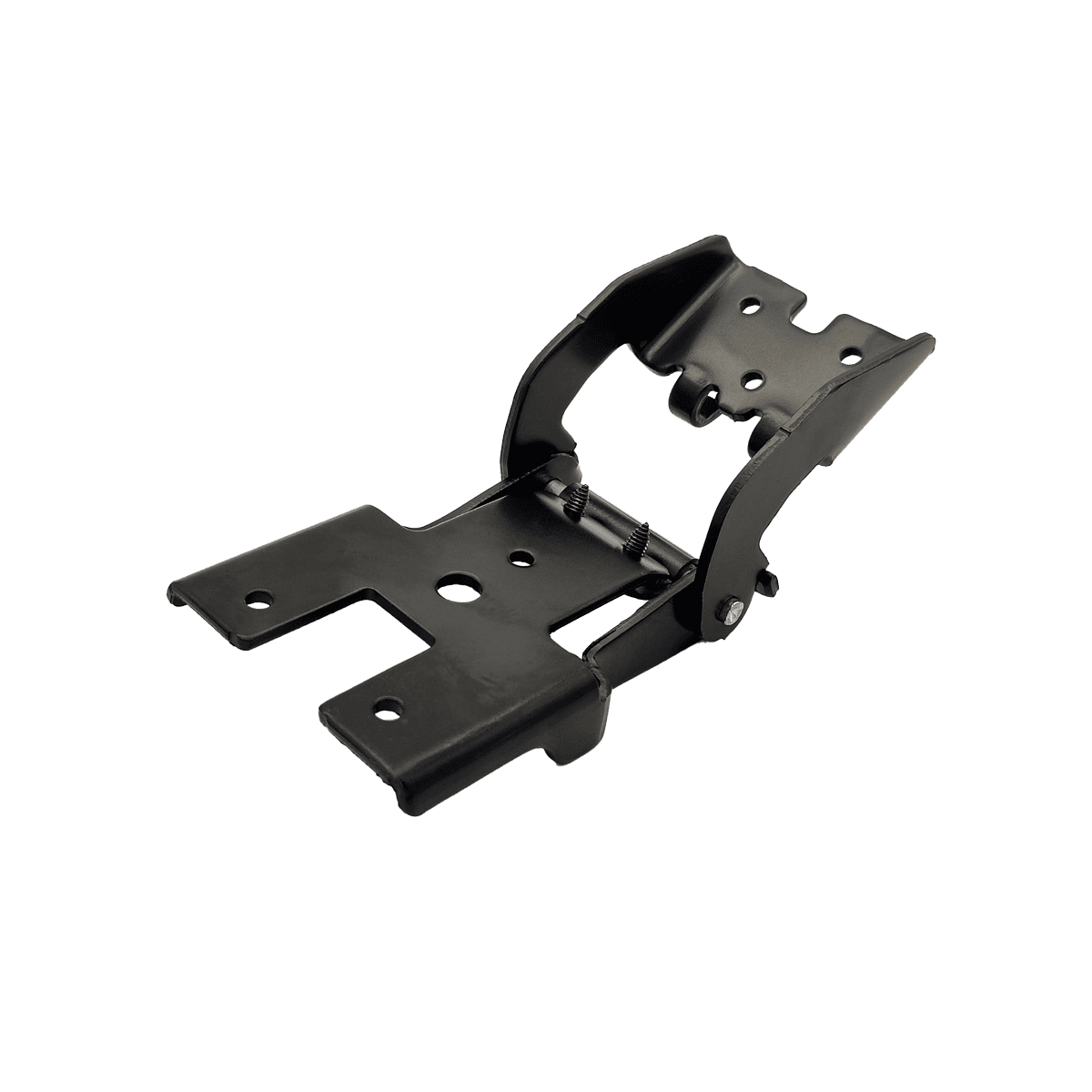
OEM: Renault
Material: DD13
Thickness: 3 mm
Annual production: 100.000
Surface treatment: Cataphoresis
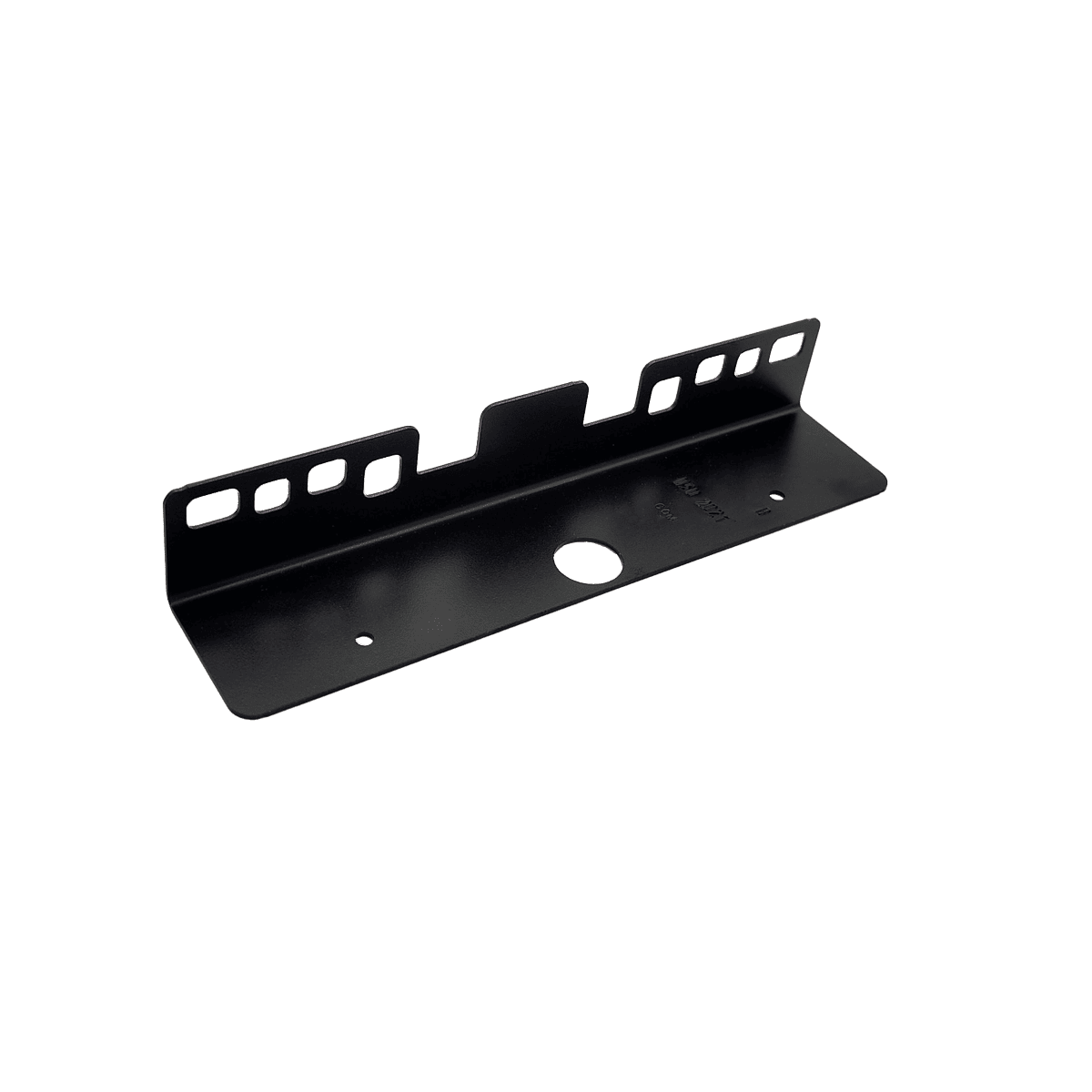
OEM: Renault
Material: HC42LA
Thickness: 1 mm
Annual production: 200.000
Surface treatment: Cataphoresis
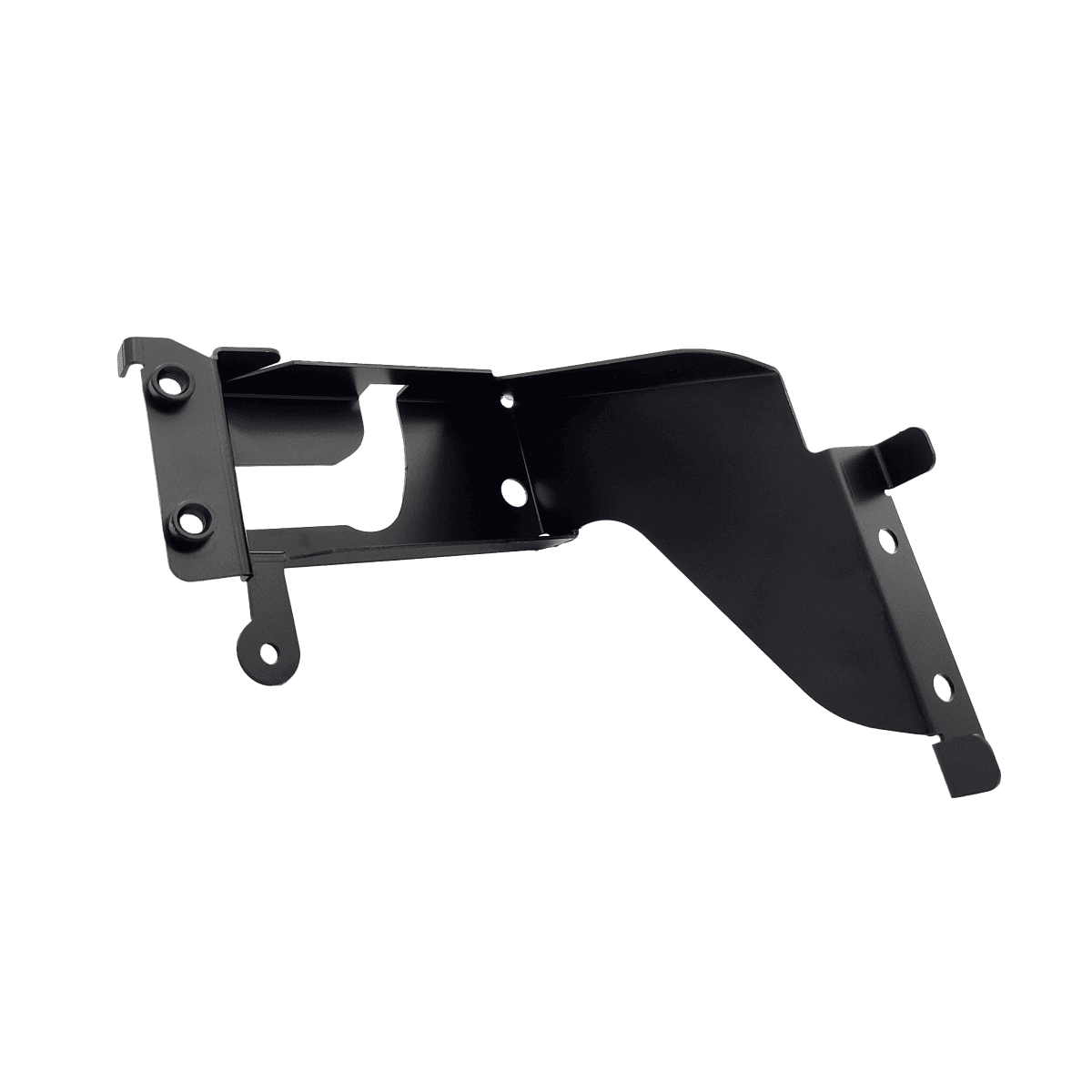
OEM: Renault trucks
Material: S420MC
Thickness: 1,5 mm
Annual production: 1.800
Surface treatment: Cataphoresis
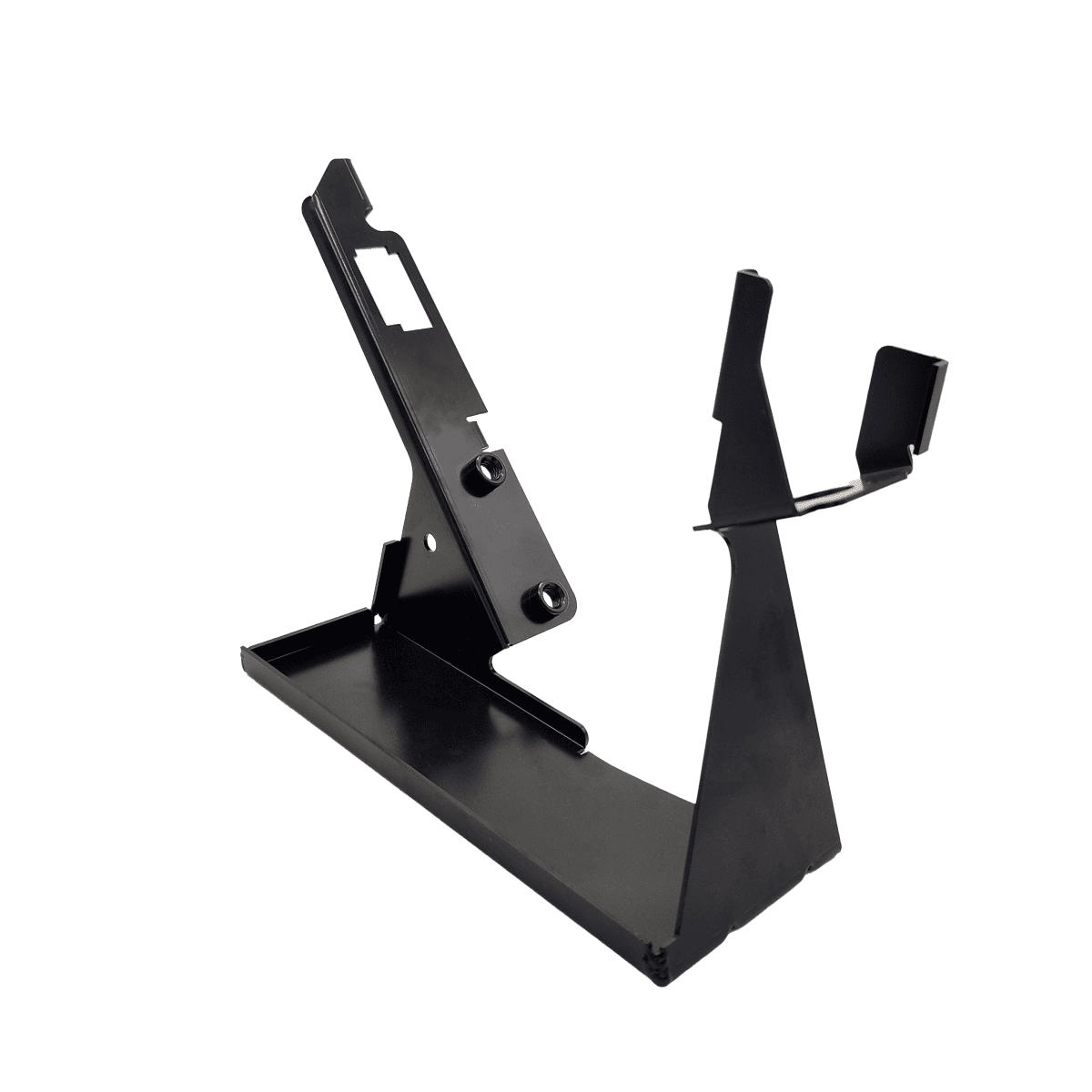
OEM: Renault trucks
Material: S420MC
Thickness: 1,5 mm
Annual production: 1.800
Surface treatment: Cataphoresis
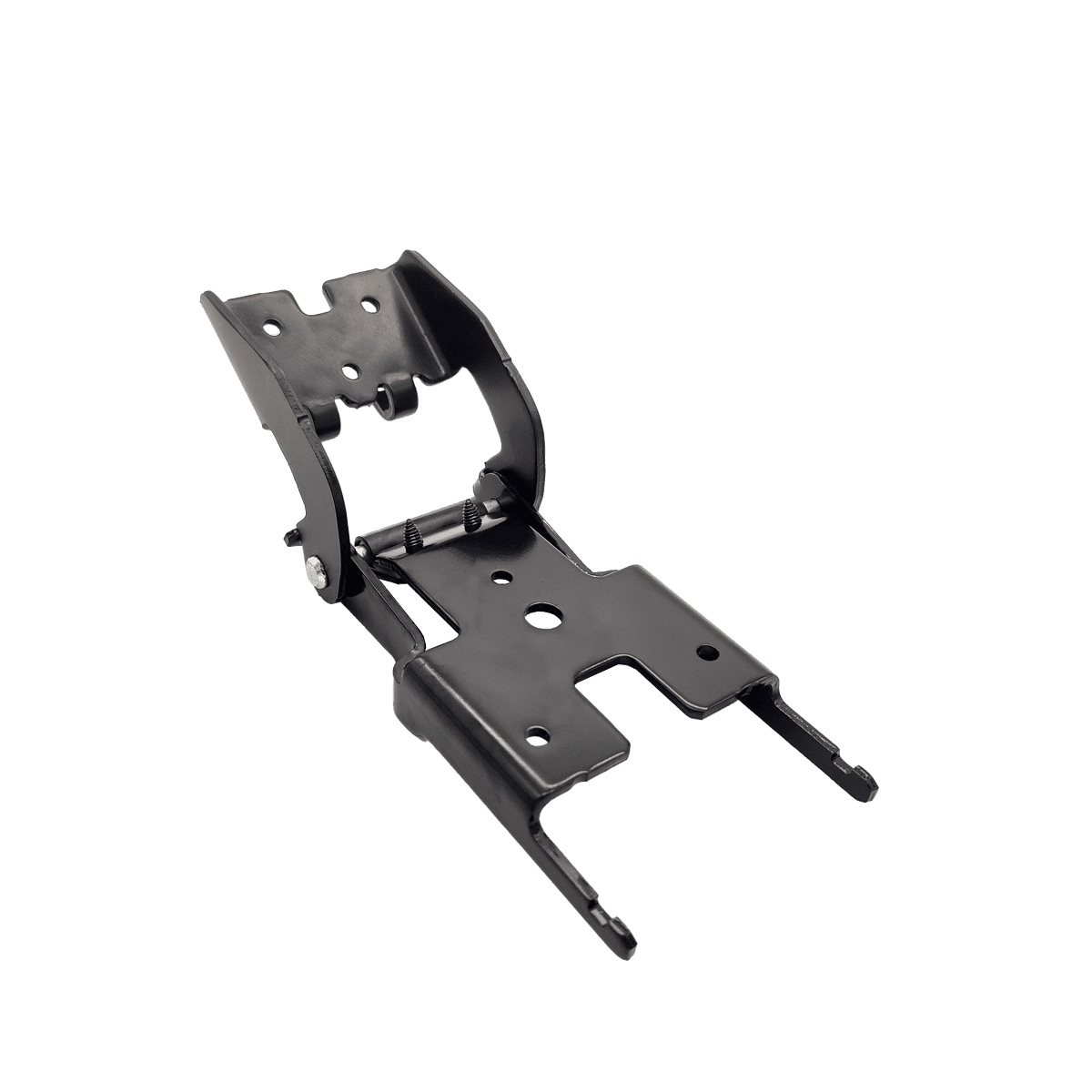
OEM: Renault
Material: DD13
Thickness: 3 mm
Annual production: 150.000
Surface treatment: Cataphoresis
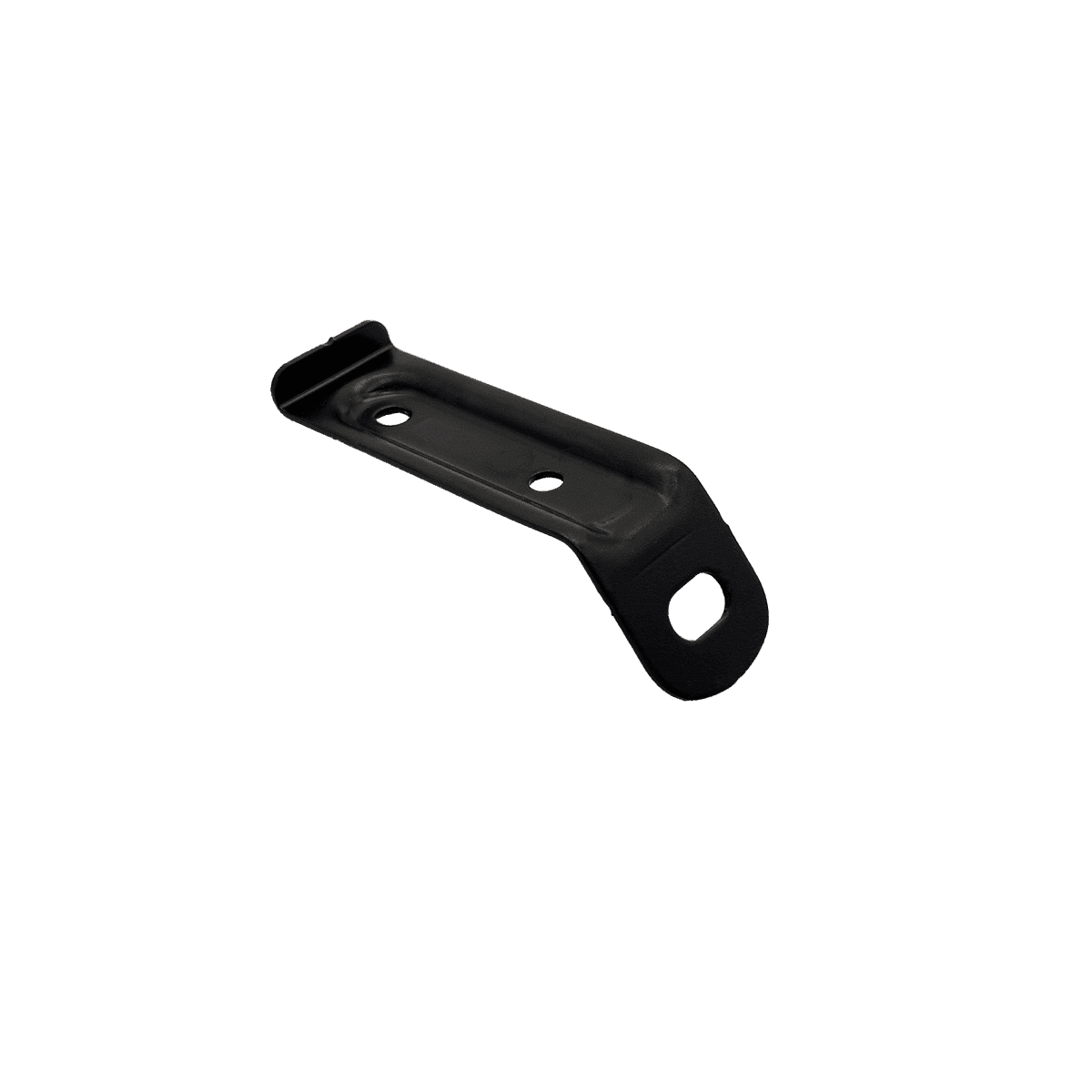
OEM: Daimler
Material: HC380LA
Thickness: 1,5 mm
Annual production: 200.000
Surface treatment: Cataphoresis
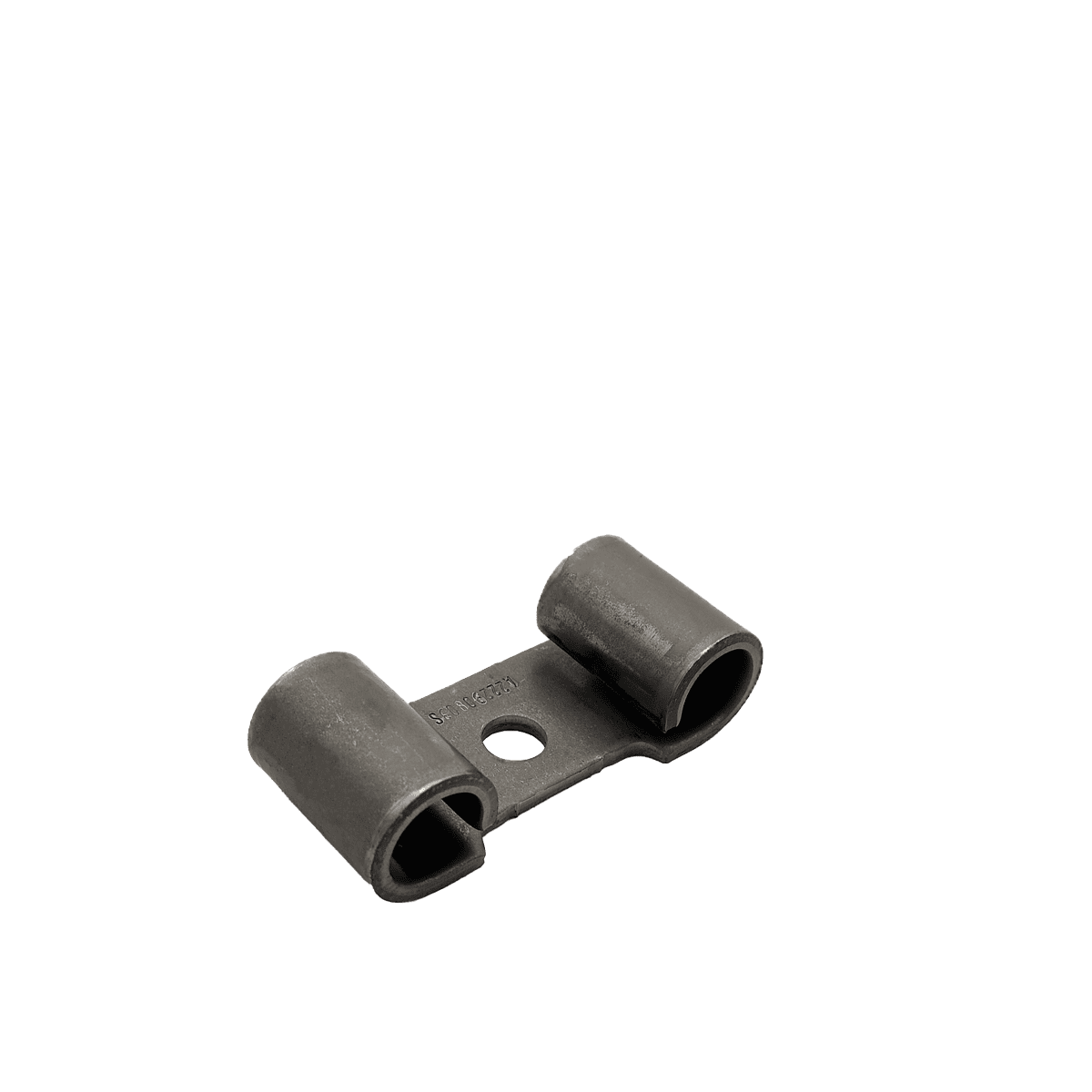
OEM: Volkswagen
Material: S355MC
Thickness: 4mm
Annual production: 1.100.000
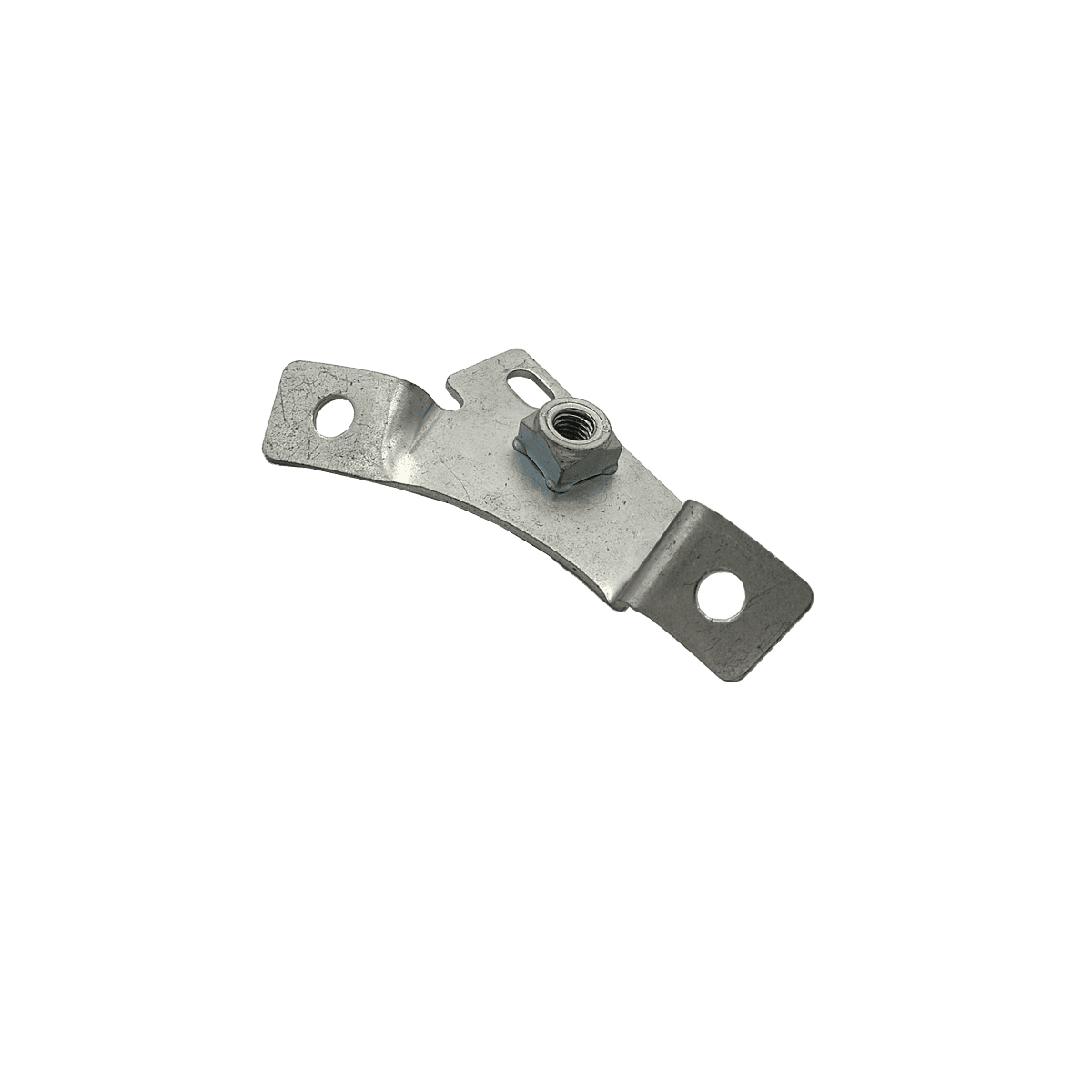
OEM: Volkswagen
Material: S420MC
Thickness: 2 mm
Annual production: 7.400
Surface treatment: Zinc
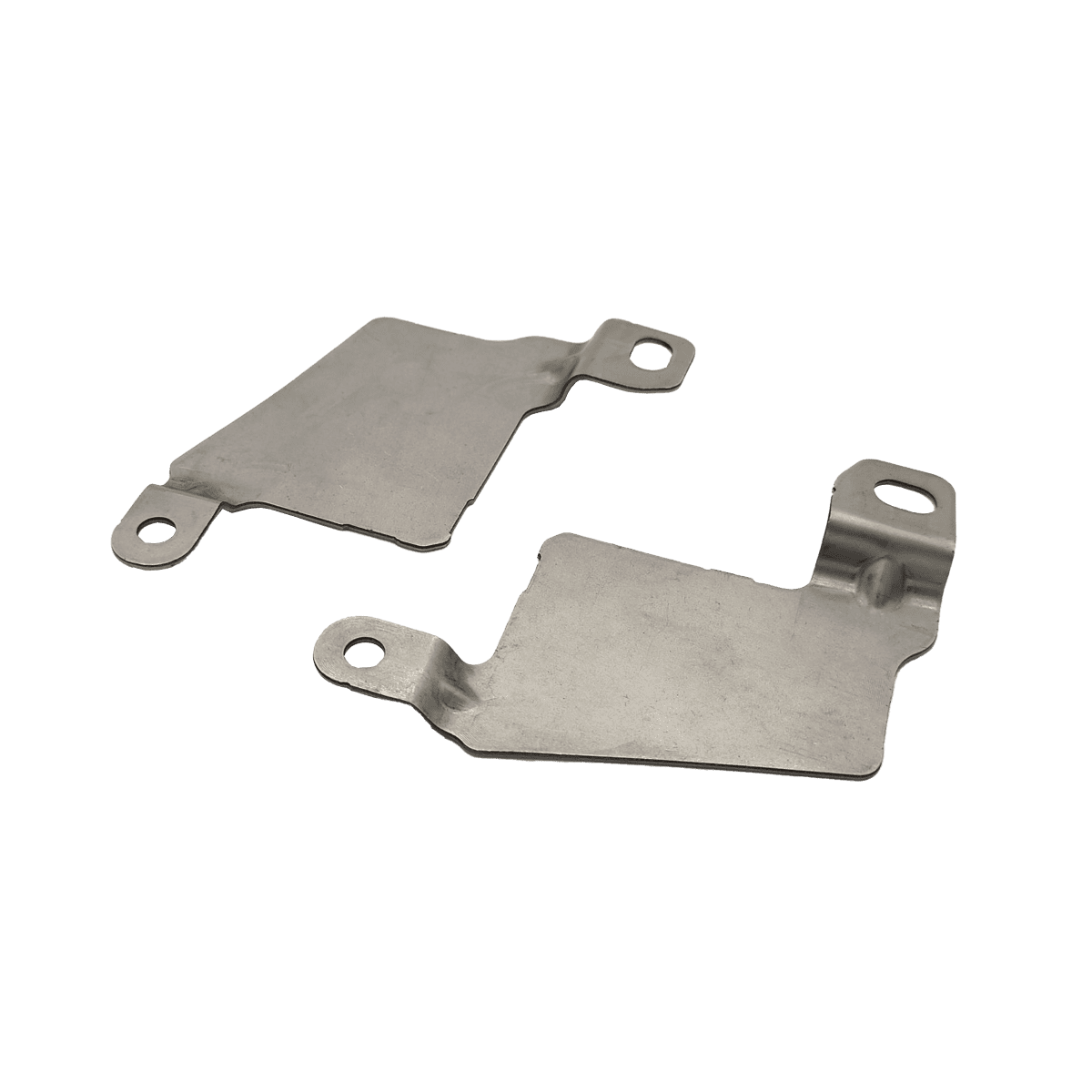
OEM: Volkswagen
Material: CR380LA
Thickness: 1,5 mm
Annual production: 300.000 (1+1)
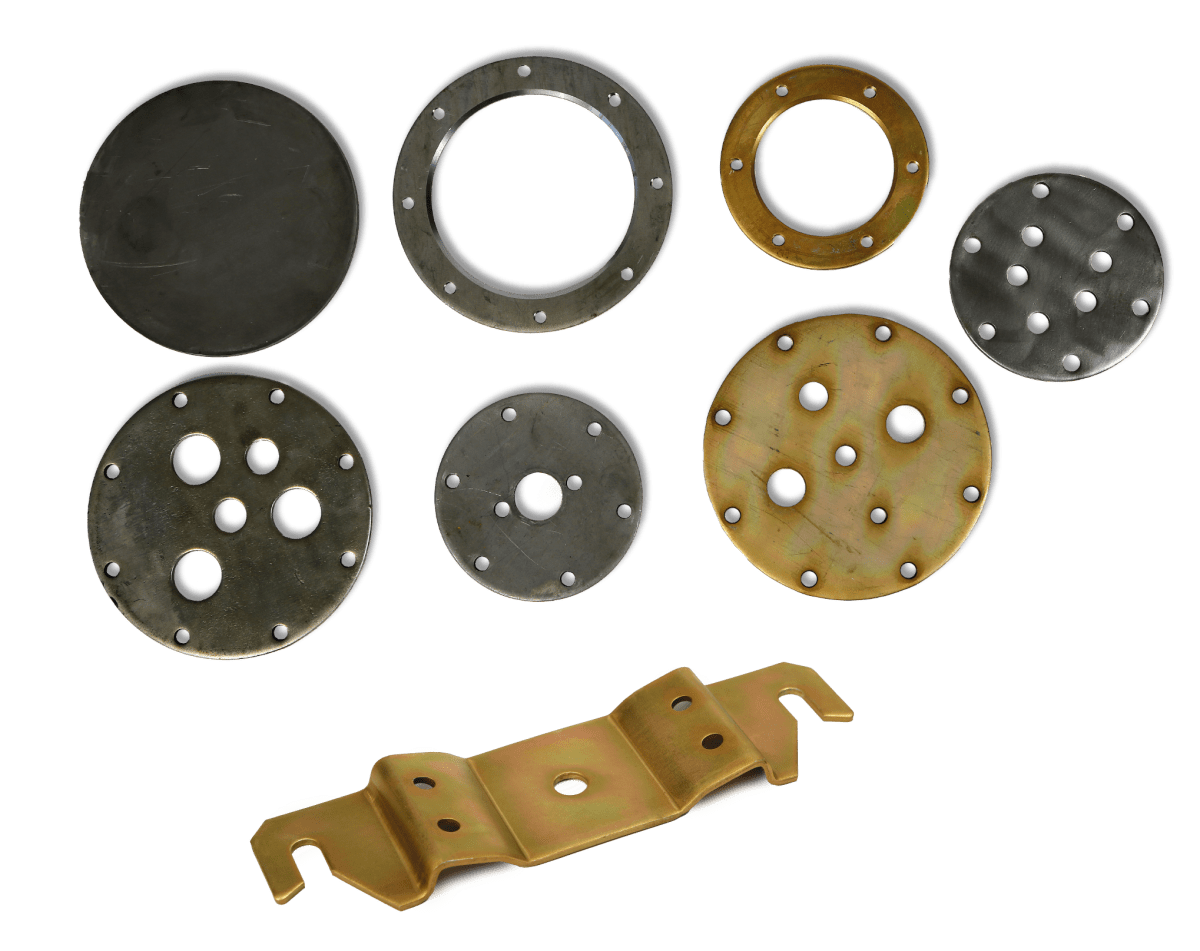
SIPEJMA
Material: Varios (S275JR, St 33, S185, P355N)
Thickness: 3 / 8 mm
Annual production: varios
Surface treatment: Zinc
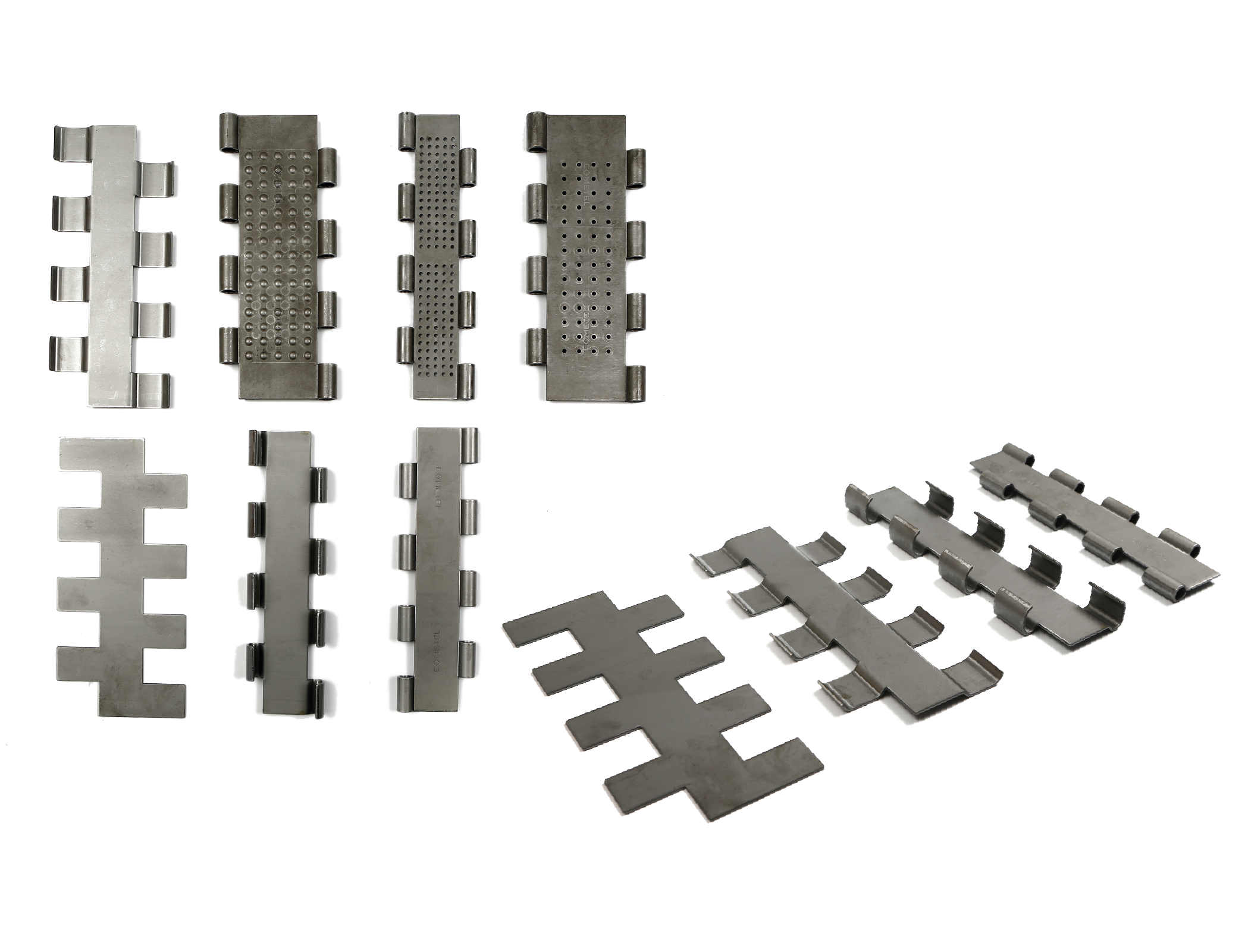
COMETEL
Material: Various (S275JR, DD11)
Thickness: 2 / 6 mm
Annual production: Various
Surface treatment: N/A
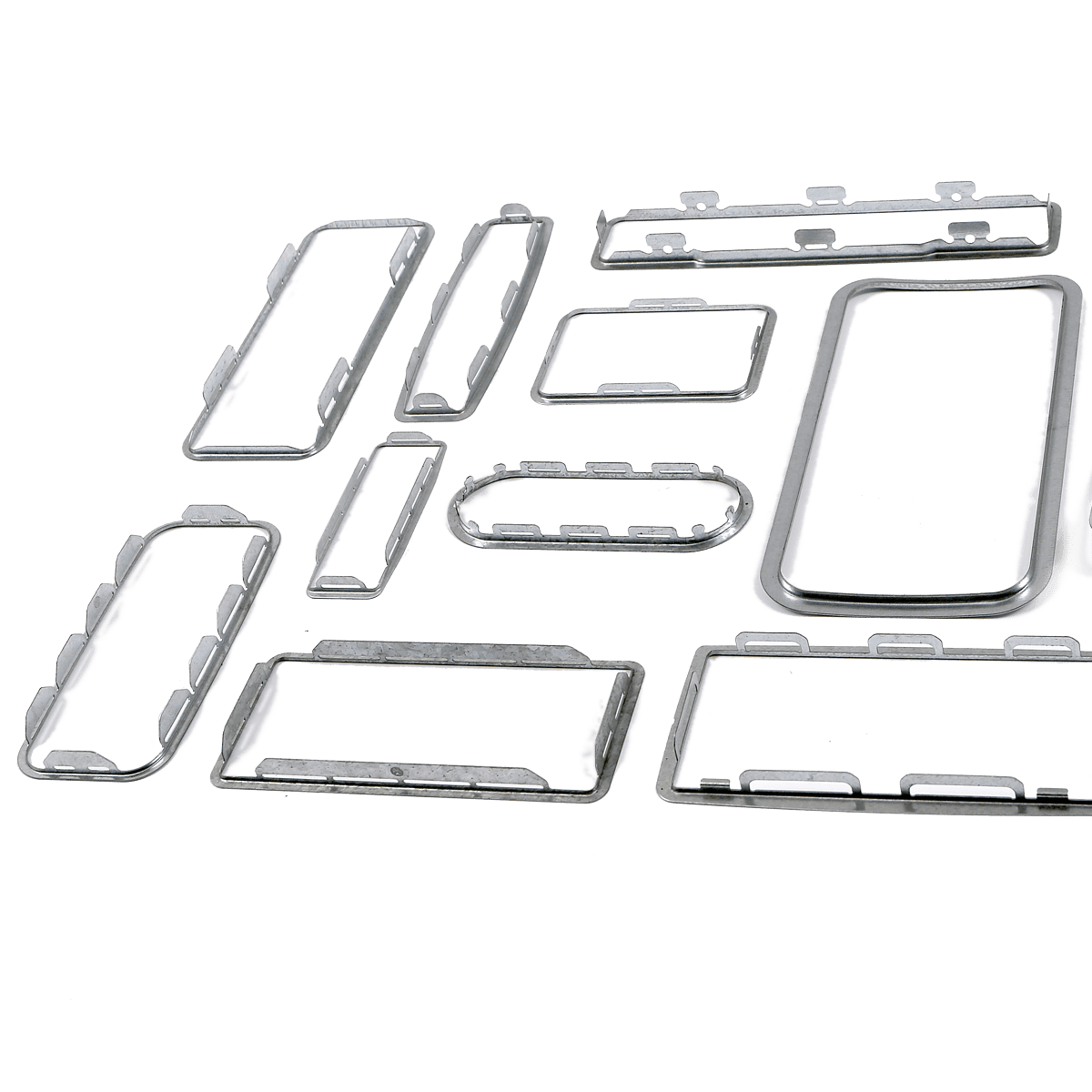
OEM: Ford, Volkswagen, Audi...
Material: Various (DX51D, DX52D)
Thickness: 0,5 / 0,7 mm
Annual production: Various
Surface treatment: Zinc
Discover our Advanced Metal Stamping Solutions
We help you create high-quality, precision metal parts tailored to your needs and budget. Download our portfolio of services and solutions and discover everything we can offer.